Im brasilianischen Werk Resende baut die TRATON Marke Volkswagen Caminhões e Ônibus (VWCO) die Lkw der Baureihe Meteor in einer vollkommen neuen Produktionsanlage. Die nach dem Industrie 4.0-Prinzip entwickelte Montagelinie ermöglicht es unter anderem, die Fahrzeuge noch individueller als bislang zu fertigen.
Von außen betrachtet wirkt sie wie ein ganz gewöhnlicher Anbau an den Teil der Fabrik von Volkswagen Caminhões e Ônibus (VWCO), in dem seit 25 Jahren Busse und Lkw vom Band laufen. Doch wer die neue Produktionshalle im brasilianischen Resende betritt, der spürt sofort, dass hier gerade ein Generationensprung in der Montage stattfindet. Der deutlichste Hinweis ist akustischer Natur: An der Produktionslinie für die Kabine des neuen, extraschweren Lkw Meteor geht es viel leiser zu als nebenan. Ein Grund dafür ist, dass VWCO bei der Meteor-Montage vollständig auf lautstarke, pneumatisch angetriebene Werkzeuge verzichtet. „Alle Bauteile werden hier elektronisch verschraubt“, berichtet Carlos Chiesse, einer der Produktionsplaner im Werk. Das leise Surren der elektrischen Werkzeuge ersetzt die typischen Zischlaute der Druckluft.
Montagelinie mit Gedächtnis
Die neue Fügetechnik schont nicht nur die Ohren von Mitarbeitern und Besuchern. Durch den elektronisch gesteuerten Vorgang kann auch das exakte Drehmoment, mit dem eine Schraube angezogen wird, eingestellt und protokolliert werden. Sämtliche Arbeitsschritte und Produktionsdaten werden anschließend im Rechenzentrum des VWCO-Werks verarbeitet und gespeichert – ein Vorgehen, das in Industrie 4.0-Betrieben inzwischen zum Standard geworden ist. Auf diese Weise wird die Fertigung mit einem Gedächtnis ausgestattet. „Wir können noch Jahre nach der Produktion nachweisen, mit welchem Drehmoment ein Teil eingeschraubt wurde“, erklärt Chiesse. „Das ist wichtig, um später Fehler nachzuvollziehen oder auszuschließen.“
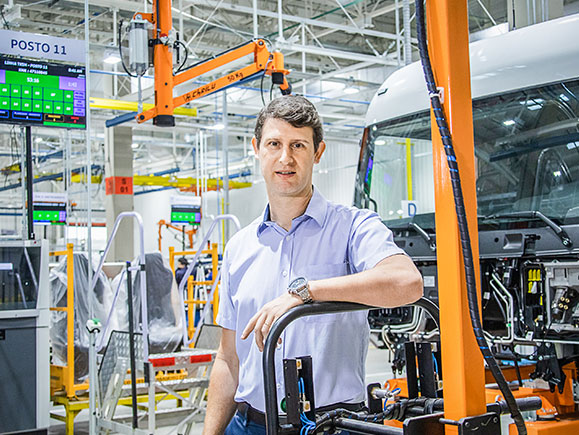
Carlos Chiesse ist einer der Produktionsplaner der neuen Montagelinie von VWCO.
„Wir können noch Jahre nach der Produktion nachweisen, mit welchem Drehmoment ein Teil eingeschraubt wurde.“CARLOS CHIESSE
Produktionsplaner VWCO
VWCO konzipierte auch die Abläufe in der Montagehalle für den Meteor neu. Statt auf einem Montageband werden beispielsweise die Kabinenteile des Lkw von einem fahrerlosen Transportfahrzeug zur nächsten Station weitergerückt. Die flache Zugmaschine wird dabei über Signalschienen im Boden gelenkt und vollautomatisch gesteuert. Zum Einsatz kommt der Digitalschlepper auf drei neuen Linien für Kabine, Motor und Chassis. Was auf den ersten Blick für mehr Aufwand sorgt, hat langfristig mehrere Vorteile, denn die Abläufe werden flexibler. Neue Bauteile oder neue Produktionsschritte lassen sich schneller in die Fertigung integrieren als bei einer traditionellen Bandproduktion. „Wir müssen dann nur das Programm wechseln und kleine Investitionen tätigen, anstatt aufwändig umzurüsten und neue Werkzeuge zu installieren“, schildert Chiesse.
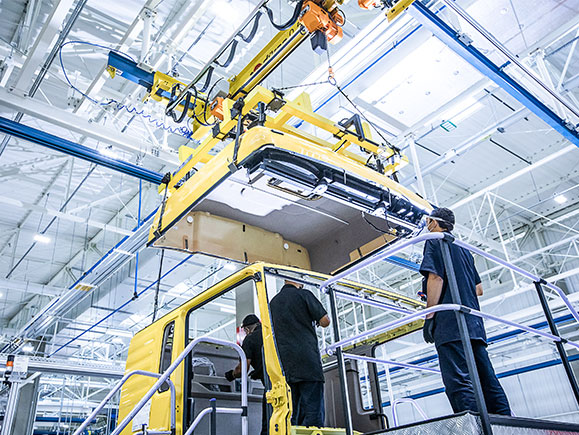
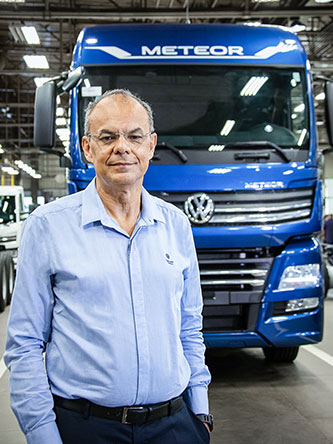
Adilson Dezoto ist stolz, die Anlage auch unter den aktuell schwierigen Bedingungen rechtzeitig in Betrieb genommen zu haben.
Erntezeit als Herausforderung
Ein wichtiger Einsatzbereich der neuen Meteor-Baureihe ist die brasilianische Soja- und Zuckerernte, zu der Farmer und Spediteure üblicherweise neue Trucks bestellen. Und die beginnt in dem südamerikanischen Land immer im Januar. Das stellte die Produktionsplaner von VWCO vor eine besondere Herausforderung: Die Anlaufphase für die Montage der extraschweren Trucks musste bis Ende Dezember 2020 abgeschlossen sein, obwohl die Corona-Pandemie die Umbauarbeiten zwischenzeitlich verzögerte. „Im April 2020 war die Fabrik in Resende beispielsweise ganz geschlossen“, berichtet Adilson Dezoto, Production & Logistics Vice President bei VWCO. „Aber wir haben den Aufbau der Anlage dennoch rechtzeitig geschafft. Ein Grund dafür ist, dass alle Beteiligten mit angepackt haben – von den Bandarbeitern über die Ingenieure bis zu Produktionsplanern und Logistikern“, sagt Dezoto nicht ohne Stolz. „Ein weiterer Grund ist die traditionell enge Zusammenarbeit mit unseren Zulieferern.“
„Im April 2020 war die Fabrik in Resende ganz geschlossen, aber wir haben den Aufbau der Anlage dennoch rechtzeitig geschafft.“ADILSON DEZOTO
Production & Logistics Vice President bei VWCO
Consórcio Modular als Schlüssel
Damit bezieht sich Dezoto auf das besondere Fabrikmodell von VWCO in Resende, das auch als Consórcio Modular bezeichnet wird. Bei diesem vor 25 Jahren etablierten Modell sind die wichtigsten Zulieferer selbstständig für ihren jeweiligen Produktionsabschnitt verantwortlich: Nicht VWCO-Mitarbeiter setzen zum Beispiel die Kabine oder den Motor ein, sondern die Kollegen der jeweiligen Zulieferer. „Dabei entwickelt VWCO mit jedem der Partner Produkte und organisiert die Montage ihrer Teile“, berichtet Dezoto. Durch das modulare und parallele Arbeiten konnte das Consórcio wertvolle Zeit gewinnen und Module wie Antrieb, Getriebe, Chassis und Kabine unabhängig voneinander vorbereiten. Durch die Erfassung der Produktionsdaten nach Industrie 4.0-Prinzipien konnte VWCO zudem die Abläufe in der Fertigung im Vorfeld der Inbetriebnahme präziser simulieren und passgenau zusammenführen.
25Vor 25 Jahren wurde das besondere Fabrikmodell „Consórcio Modular“ von VWCO in Resende etabliert.
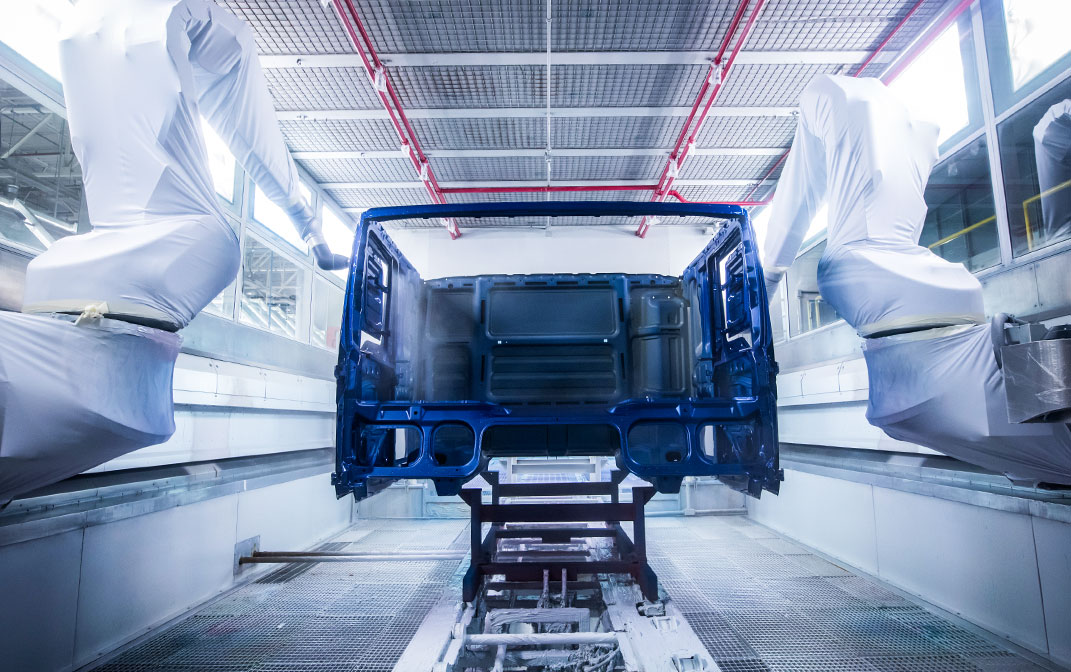
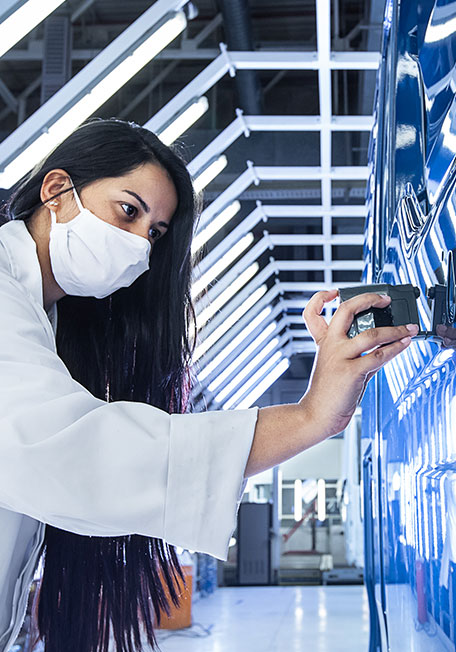
In der auf Industrie 4.0-Prinzipien ausgerichteten Anlage fließen Kundenwünsche direkt in den Produktionsprozess ein.
Trucks nach Maß
Kombiniert mit der vollständig digitalisierten Produktion ermöglicht es die modulare Montage, in der neuen Fertigungslinie den Meteor maßgeschneidert herzustellen. Denn VWCO stellt eine breitere Palette an Bauteilvarianten als bislang zur Verfügung und passt sie ständig an den Marktbedarf an. Mehr noch: Individuelle Sonderwünsche lassen sich selbst in letzter Minute noch in den Prozess integrieren. „Wenn ein Kunde im Nordosten Brasiliens seinen Meteor bestellt, dann ist es, als würde er hier im Tausende Kilometer entfernten Resende die Montage-Computer bedienen“, veranschaulicht Dezoto mit einem Augenzwinkern.
Mit einer Fahrzeugpalette von drei bis 125 Tonnen zulässigen Gesamtgewichts hat VWCO in Brasilien ein sehr breites Angebot. Als Maßanfertigung soll der Meteor möglichst viele Anforderungen im schwersten Marktsegment für Trucks bedienen. Denn je nachdem, ob das Fahrzeug im Kundeneinsatz zwei Anhänger mit Zuckerrohr zieht oder ob es Soja über eine Strecke von 2.000 Kilometern zu den Atlantikhäfen bringt, verlangt es eine völlig andere Ausstattung. „Wir haben dazu zahlreiche Nutzer befragt“, berichtet Simone Santana, Analystin im Marketing von VWCO. „Jetzt integrieren wir die Wünsche der Speditionen und Fahrer in den Produktionsprozess.“ So bietet VWCO im Meteor den Langstrecken-Fahrern zum Beispiel ein extrabreites Bett oder eine per Knopfdruck bewegbare Kühlbox an. „Wir wollen den Kunden das als Standardausstattung anbieten, was andere als Extra betrachten“, sagt Santana. Die neue Montage 4.0 in Resende macht es möglich.