The TRATON brand Volkswagen Caminhões e Ônibus (VWCO) is building the Meteor truck series in a completely new digital manufacturing facility at the plant in Resende, Brazil. The assembly line was developed according to the Industry 4.0 principle and enables, among other things, a more customized approach than ever before to manufacturing vehicles.
From the outside, it appears to be a standard addition to the part of the Volkswagen Caminhões e Ônibus (VWCO) manufacturing plant where buses and trucks have been rolling off the line for 25 years. But those who step into the new production hall in Resende, Brazil, notice right away that this truly represents a new generation of data-driven smart manufacturing. The clearest indication of this is acoustical: the assembly line for the cab of the new super heavy-duty Meteor truck is much quieter than the neighboring one. A reason for this is that when it comes to the Meteor assembly, VWCO completely moved away from deafening pneumatically powered tools. “All of the components are electronically bolted together here,” reports Carlos Chiesse, who is a manufacturing planner in the plant. Thus, the gentle humming of electric machines replaces the typical hissing of compressed air.
Assembly line with a memory
The new industrial joining technology is not only kinder to employees’ and visitors’ ears; thanks to the electronically controlled process, it can also calibrate and log the precise torque used to tighten the bolt. All the work steps and production analytics are then processed and saved in the data center of the VWCO truck manufacturing factory. This procedure has long since become a standard feature for Industry 4.0 digital technologies and serves as a kind of memory for manufacturing. “Years after production, we can still establish the torque used when a part was bolted in,” explains Chiesse. “This is important for tracing and eliminating errors later on.”
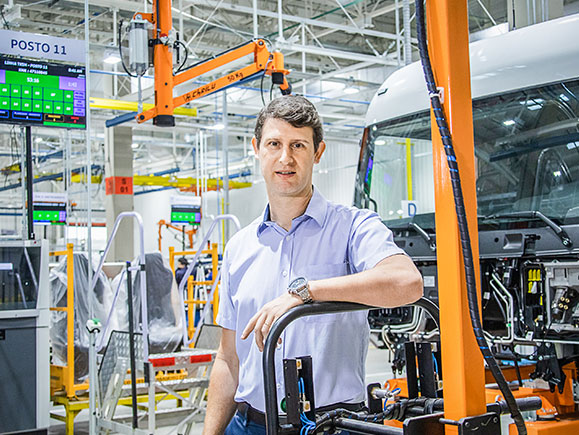
Carlos Chiesse is a manufacturing planner for the new VWCO assembly line.
“Years after production, we can still establish the torque used when a part was bolted in.”CARLOS CHIESSE
Manufacturing planner at VWCO
VWCO also developed new concepts for the processes in the assembly hall for the Meteor. Instead of using an assembly line, the cab parts of the truck are moved from one workstation to the next with the help of a self-driving transport vehicle. The flat tractor is guided by a signal busbar located in the floor and is controlled fully automatically. The digital tractor is used in connection with three new lines for the driver cab, engine, and chassis. Although this may appear more complicated at first glance, it increases the flexibility of the processes, thus offering several advantages in the long term. New components or production steps can be integrated into manufacturing more quickly than in traditional line production. “Then all we have to do is change the program and make small investments, instead of having to put a lot of effort into retooling and installing new equipment,” explains Chiesse.
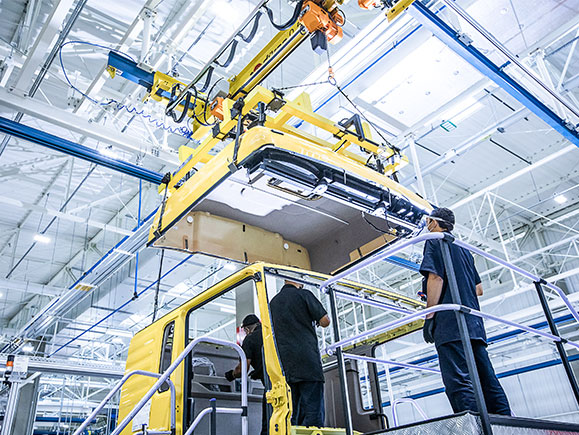
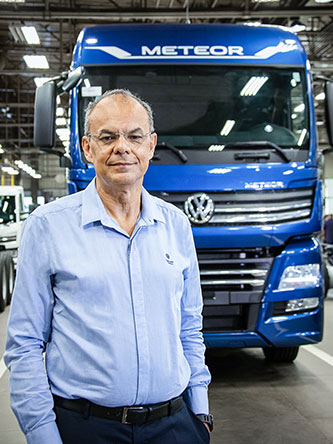
Adilson Dezoto is proud of getting the line up and running on time, despite ongoing difficult conditions.
The challenge of harvest time
One important field of application for the new Meteor series is the Brazilian soy and sugar harvest, for which farmers and freight forwarders usually order new trucks. The harvest always begins in January in Brazil, which poses a particular challenge for the production planners from VWCO. The ramp-up phase of the assembly of the company’s super heavy-duty trucks had to be finished by the end of December 2020, even though the restructuring measures were delayed by the COVID-19 pandemic. “For instance, the factory in Resende was even closed entirely in April 2020,” explains Adilson Dezoto, Production & Logistics Vice President at VWCO. “But we still managed to finish restructuring the factory on time. One reason is that everyone involved pitched in — from the assembly line workers to the engineering staff to the production planners and logistics specialists,” states Dezoto proudly. “Another reason is the traditionally close collaboration with our suppliers.”
“The factory in Resende was even closed entirely in April 2020. But we still managed to finish restructuring the factory on time.”ADILSON DEZOTO
Production & Logistics Vice President at VWCO
Consórcio Modular as the key
Dezoto is referring to the special factory model from VWCO in Resende, also called Consórcio Modular. It was established 25 years ago and includes the most important suppliers, who are independently responsible for their respective stages of production: for example, it isn’t the VWCO employees who are responsible for installing the cab or engine, but rather the employees of the respective supplier. “Throughout the process, VWCO develops products with each partner and organizes the installation of their parts,” reports Dezoto. Thanks to this modular and parallel approach to work, the Consórcio was able to gain valuable time and prepare modules such as the drive system, transmission system, chassis, and cab independently of each other. The recording of production analytics according to Industry 4.0 principles also allowed VWCO to more precisely simulate and perfectly merge the manufacturing processes prior to the start of production.
2525 years ago, the special factory model "Consórcio Modular" was established by VWCO in Resende.
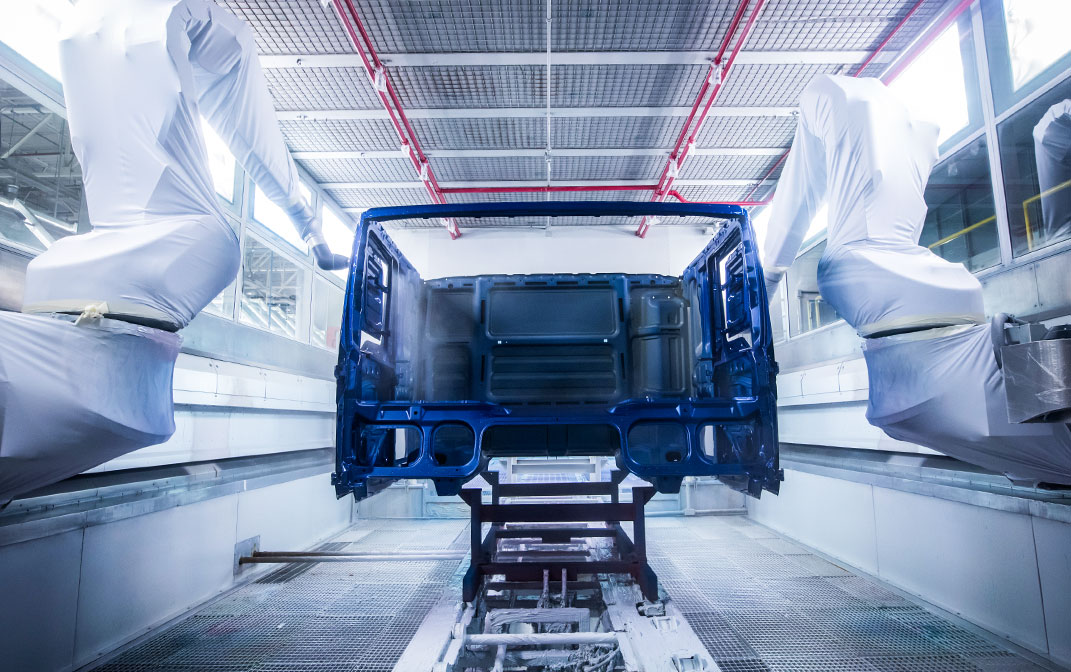
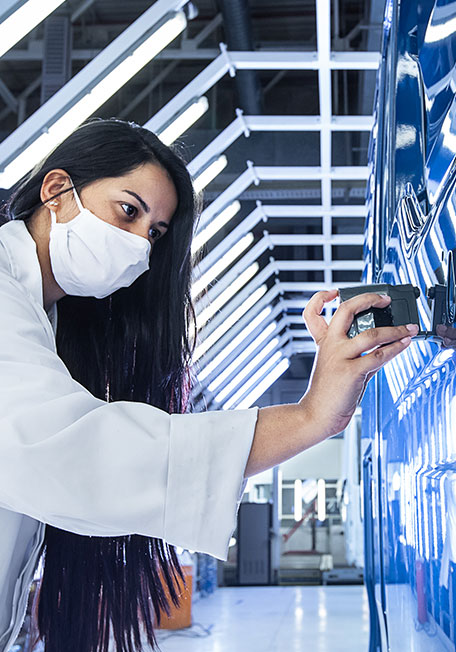
Customers’ requests are integrated directly into the production process at this facility, which was developed according to Industry 4.0 principles.
Customized trucks
Combined with completely digitalized production, the modular assembly enables the customized manufacturing of the Meteor directly in the new production line. That is because VWCO has developed a wider range of components than before and adapts them continually to reflect market demand. What is more, customized extras can be integrated into the process in the smart factory right up to the last minute. “When a customer in Northeast Brazil orders a Meteor, it is almost as if they are operating the assembly computer located thousands of kilometers away here in Resende,” explains Dezoto with a twinkle in his eye.
With a vehicle range of three to 125 tons of permissible total weight, VWCO offers a broad portfolio in Brazil. As a customized vehicle, Meteor is intended to fulfill the widest variety of demands in the most challenging market segment for trucks. That is because entirely different configurations are required depending on whether the customer uses the vehicle to transport two trailers with sugarcane or to haul soy over a 2,000-kilometer route to reach the Atlantic Ocean ports. “We surveyed numerous users about this,” reports Simone Santana, who is a marketing analyst at VWCO. “Now we are integrating the wishes of freight forwarders and drivers into the production process.” Thus, when it comes to the Meteor, the truck manufacturer offers long-haul drivers an extra-wide bed or a cooler that moves at the touch of a button, for example. “What others see as extras are things we offer our customers as standard features,” says Santana. The new assembly 4.0 in Resende is making this possible.