Modularität und gruppenweite Baukästen sind Schlüsselfaktoren für den künftigen Erfolg von TRATON. Einen Ausblick darauf, wie elektrische Antriebe gemeinsam entwickelt und produziert werden, gibt ausgerechnet ein Diesel: Der neue 13-Liter-Basismotor Common Base Engine ist der letzte Verbrenner der TRATON GROUP und gleichzeitig der erste Antrieb, der markenübergreifend entstanden ist.
Das Grundprinzip von Modularität ist ganz einfach: Hersteller konzipieren ihre Produkte so, dass sie aus Bausteinen je nach Kundenanforderung individuell zusammengesetzt werden können. Das Verwenden solcher Bausteine vereinfacht die Entwicklung und spart auch in der Produktion Kosten. Scania nutzt diese Vorteile schon seit fast einem Jahrhundert, seit etwa 40 Jahren setzen die Schweden vollständig auf ein modulares Baukastensystem. Das Byggladan-Prinzip, abgeleitet vom schwedischen Wort für Baukasten, war auch bei der Entwicklung des Common Base Engine, kurz CBE, von Anfang an wesentlich.
Der CBE ist das neue 13-Liter-Dieselaggregat der TRATON GROUP. Er wird in Europa, Nord- und Südamerika und potenziell auch in China in schweren Lkw und Bussen zum Einsatz kommen. Und er wird auch dort vor Ort gefertigt werden: von Scania in Schweden, Navistar in den USA, MAN in Deutschland und Volkswagen Truck & Bus in Brasilien. Dank des Baukastenprinzips sind dabei 80 Prozent des Motors überall gleich, die übrigen 20 Prozent betreffen Komponenten, mit denen die Marken den CBE für die besonderen Anforderungen der Kunden in ihren jeweiligen Märkten individualisieren können. Eine solche Anforderung ergibt sich zum Beispiel aus gesetzlichen Vorgaben hinsichtlich der Abgaswerte, die je nach Land unterschiedlich ausfallen können.
„Bei dem neuen Motor ging es vor allem darum, Kraftstoff und CO2-Emissionen einzusparen.“Magnus Henrikson
Chefingenieur bei Scania
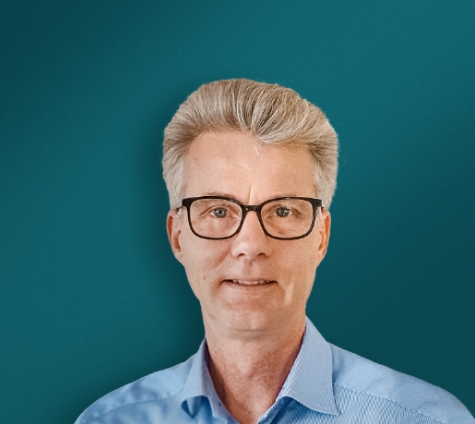
Magnus Henrikson, Chefingenieur bei Scania
Vom Scania- zum TRATON-Motor
„Das erste Mal nachgedacht über einen neuen Motor haben wir schon im Jahr 2008“, erinnert sich Magnus Henrikson, Chefingenieur bei Scania. „Richtig los ging es dann hier mit einem Konzept im April 2012.“ Henrikson ist seit 32 Jahren bei Scania, den CBE hat er vom White Paper bis hin zur Fertigung begleitet. „Bei dem neuen Motor ging es vor allem darum, Kraftstoff und CO2-Emissionen einzusparen“, erklärt der Ingenieur. Anfang 2015 bekommt die Entwicklung eine neue Richtung: MAN und Scania werden Schwestermarken – und Henrikson soll das neue Aggregat fortan gemeinsam mit den Kollegen aus Deutschland entwickeln. „Am Anfang war die Zusammenarbeit nicht leicht, auf beiden Seiten ging es viel um Ansehen“, weiß Henrikson noch.
Thomas Nickels erinnert sich gut an diese Anfangsphase der TRATON GROUP. Als Head of Powertrain bei MAN war er dafür zuständig, in der Konzeptphase die Anforderungen von MAN einzubringen: „Wir haben versucht, alle Experten von Scania und MAN mit ins Boot zu holen.“ Die Zusammenarbeit beginnt nicht ohne Reibungen, es finden viele gemeinsame Workshops statt. „Wir haben uns damals intensiv miteinander auseinandergesetzt und mussten einiges neu entwickeln“, erzählt Håkan Johansson, der in dieser Phase als Head of Conventional Powertrain bei Scania zum Projekt kommt. „In dieser Zeit ist aus dem Scania-Motor ein TRATON-Motor geworden. Wir haben viel und auch kontrovers diskutiert, aber am Schluss hatten wir einen besseren Motor.” Der CBE ist im Vergleich zum ersten Konzept kürzer, leichter, spart noch mehr Treibstoff und kostet weniger.
„Wir haben uns damals intensiv miteinander auseinandergesetzt und mussten einiges neu entwickeln.“Håkan Johansson
Head of Conventional Powertrain bei Scania
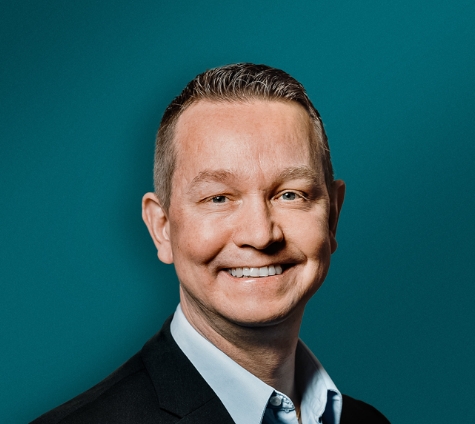
Gleich aber verschieden
Neben grundlegenden Eigenschaften des Motors wie Größe, Gewicht oder Verbrauch spielt seine spätere Integrierbarkeit eine entscheidende Rolle: „Unser Fokus lag auch darauf, den späteren Integrationsaufwand in die Fahrzeuge von MAN so gering wie möglich zu halten“, erklärt Nickels. „Das war eine sehr große Herausforderung.“ Auf der einen Seite sollte es möglichst viele gemeinsame Bauteile und Komponenten geben, auf der anderen möglichst geringe Auswirkungen auf der Fahrzeugseite. „Die Fahrzeuge sind von außen betrachtet ähnlich, sie haben den gleichen Radstand und die gleichen Abmessungen“, so Nickels. „Im Detail sind Fahrzeuggestaltung und die Anwendung im Fahrzeug bei Scania und MAN doch recht unterschiedlich.“
Der Spagat zwischen möglichst vielen gemeinsamen Bauteilen und möglichst geringen Auswirkungen auf das Fahrzeug betrifft aber nicht nur den Motor, er betrifft den gesamten Antriebsstrang. Achse, Abgasnachbehandlung oder Steuerelektronik: Auch hier wird es in Zukunft unter dem Namen Future Powertrain Program (FPP) einen gemeinsamen Baukasten für alle Marken geben. Damit der Motor und gesamte Antriebstrang in die Fahrzeuge der verschiedenen Marken eingebaut werden können, müssen die Ingenieure die Schnittstellen anpassen. „Wenn ich zum Beispiel Anbauteile für den Motor entwickle, dann gestalte ich sie so, dass sie möglichst bei jeder Marke an derselben Stelle positioniert sind“, erklärt Nickels. Die Bauteile müssen den individuellen Anforderungen der jeweiligen Fahrzeuge gerecht werden ohne, dass neue Varianten dieser Teile notwendig werden. „Das ist eine große Herausforderung.“
„Wir haben versucht, alle Experten von Scania und MAN mit ins Boot zu holen.“Thomas Nickels
Head of Electrification Development Group Industrial Operations TRATON SE, Senior Vice President Engineering Drivetrain, Cabin & Chassis (ED) MAN Truck & Bus SE
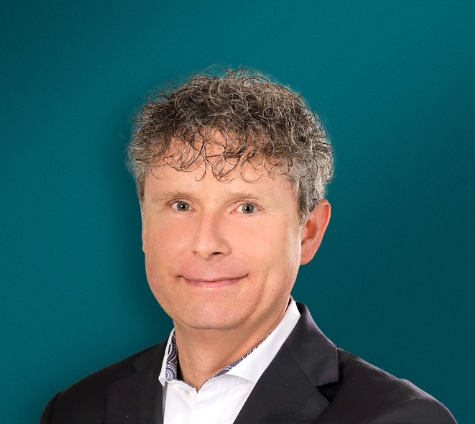

Darren Gosbee, Vice President of Engineering in der Forschung und Entwicklung bei Navistar
Neue Baukästen
Vor dieser Herausforderung stand auch Navistar, das Unternehmen ist seit 2017 am CBE-Projekt beteiligt. Damals war es noch Partner der TRATON GROUP, seit 2021 gehört es als Tochter zur Gruppe. Der CBE kommt mit einem sogenannten Long Mount, Navistar verwendet traditionell einen Short Mount. „Der Unterschied ist deutlich zu sehen, wenn man die Frontpartie eines US-Trucks mit der eines aus Europa vergleicht“, erklärt Darren Gosbee, Vice President of Engineering in der Forschung und Entwicklung bei Navistar. Dadurch wird eine andere Aufhängung des Motors notwendig. Die Ingenieure bei Navistar haben hart an den Schnittstellen zu ihren Produkten gearbeitet. Und das mit Erfolg. Ein Baukasten sei eine gute Möglichkeit, Komplexität zu managen, so Gosbee: „Wir denken bereits darüber nach, wie wir unsere Fahrzeugdesigns so anpassen können, dass wir in Zukunft mehr gemeinsame Teile übernehmen können.“ Bis dahin gelte es, noch mehr über Modularität zu lernen und weiter zu wachsen.
Auch für Nickels ist die Baukastenidee, wie sie jetzt beim FPP und CBE markenübergreifend zum Tragen kommt, ausbaufähig: „Wenn wir auf gemeinsame umfangreichere Systeme gehen, wie zum Beispiel das Chassis, gibt es weitere, enorme Einsparpotenziale. Dann entfällt zum Beispiel die Anpassung der Schnittstellen, wenn wir diese für alle Marken angleichen. Dadurch kann der Baukasten kleiner werden, das bedeutet noch weniger Komplexität bei niedrigeren Kosten.“
„Wir denken bereits darüber nach, wie wir in Zukunft mehr gemeinsame Teile übernehmen können.“Darren Gosbee
Vice President of Engineering in der Forschung und Entwicklung bei Navistar
Die Zukunft der Modularität
Gleiche Schnittstellen und möglichst kleine Baukästen sind auch im Hinblick auf die E-Mobilität interessant. Gerade im Nutzfahrzeugbereich geht es bei elektrischen Antrieben um Reichweite, und die hängt unmittelbar mit dem Batteriepack zusammen. „Wenn wir uns anschauen, wie Batterien am besten verbaut werden, sind wir wieder tief im Thema Schnittstelle zwischen Komponente und Fahrzeug“, sagt Nickels. „Hier haben wir ein tolles Projekt durchgeführt, bei dem wir einen gemeinsamen Baukasten für Batterien mit Scania, MAN, Navistar und Volkswagen Truck & Bus abgestimmt und entwickelt haben.“ Ein Beispiel, wie die Umstellung auf E-Mobilität in der TRATON GROUP die Chance bietet, die Entwicklung neuer Produkte auf einer Plattform statt auf vielen zu beginnen.
Bis sich die E-Mobilität flächendeckend durchsetzt, wird es noch dauern, für einige Anwendungen und in bestimmten Regionen können noch Jahrzehnte vergehen. Der CBE mag also der letzte Dieselmotor der Gruppe sein, ein Auslaufmodell ist er nicht: Schon 2025 soll jeder zweite schwere Lkw der TRATON GROUP mit CBE ausgeliefert werden. Seine Prämiere auf der Straße feiert der neue Motor bei Scania: Der 460 R Highline ist das erste Fahrzeug, das von dem gemeinsam entwickelten Aggregat angetrieben wird. Im Februar 2022 überzeugte der Lkw mit dem CBE beim europaweit renommierten 1.000-Punkte-Test als klarer Sieger. 2023 wird Navistar den CBE einführen, MAN folgt ein Jahr später, 2028 dann auch Volkswagen Truck & Bus. Im Vergleich zu den Motoren, die er ablöst, hat der CBE einen höheren Wirkungsgrad von über 50 Prozent. Er verbraucht bis zu acht Prozent weniger Treibstoff, bietet eine höhere Gesamtwirtschaftlichkeit und verursacht erheblich weniger CO2-Emissionen.
Bei der Entwicklung des CBE haben die Marken viel gelernt, und bei seiner Einführung über Marken- und Ländergrenzen hinweg werden sie weiter Erfahrungen sammeln. Davon profitiert die TRATON GROUP auch für die künftige Entwicklung von E-Antrieben. Und sie hat die Chance, Neuentwicklungen auf einer Plattform zu beginnen und sich die aufwändige Integration in verschiedene Fahrwerke zu sparen. Das Thema Modularität erreicht so gruppenweit die nächste Stufe.