Mit ihrem futuristischen Erscheinungsbild und ihrem relativ neuen Marktauftritt scheinen BEVs ein modernes Phänomen zu sein. Sie haben jedoch erstaunliche historische Wurzeln, denn die ersten Elektroautos wurden bereits in den 1820er-Jahren eingesetzt. Der erste Elektrobus von Scania, der Scania-Vabis T31, kam 1940 auf den Markt, während MAN seinen allerersten vollelektrischen Bus, den 750 HO-M10 E, 1970 vorstellte.
Diese frühen EV-Entwicklungen haben den Weg für die batteriebetriebenen Mobilitätslösungen von heute vorbereitet, bei denen das gestiegene Bewusstsein und die Besorgnis über den Klimawandel zusammen mit regulatorischen Faktoren und technologischen Innovationen einen bemerkenswerten Wandel im elektrifizierten Verkehr vorantreiben. In den letzten zehn Jahren hat sich der Übergang von Verbrennungsmotoren hin zur Elektrifizierung deutlich beschleunigt. Die TRATON GROUP treibt diesen Wandel mit ihren Marken Scania, MAN, Navistar und Volkswagen Truck & Bus (VWTB) voran. So gründete TRATON im Jahr 2022 das Lade-Joint-Venture Milence, während Scania im September 2023 die Einweihung seiner Batteriemontage in Södertälje feierte. In Kürze wird eine neue Generation von Batterien eingeführt, die eine neue Ära des elektrischen Verkehrs einläuten wird.
Die Herausforderungen für kommerzielle BEVs
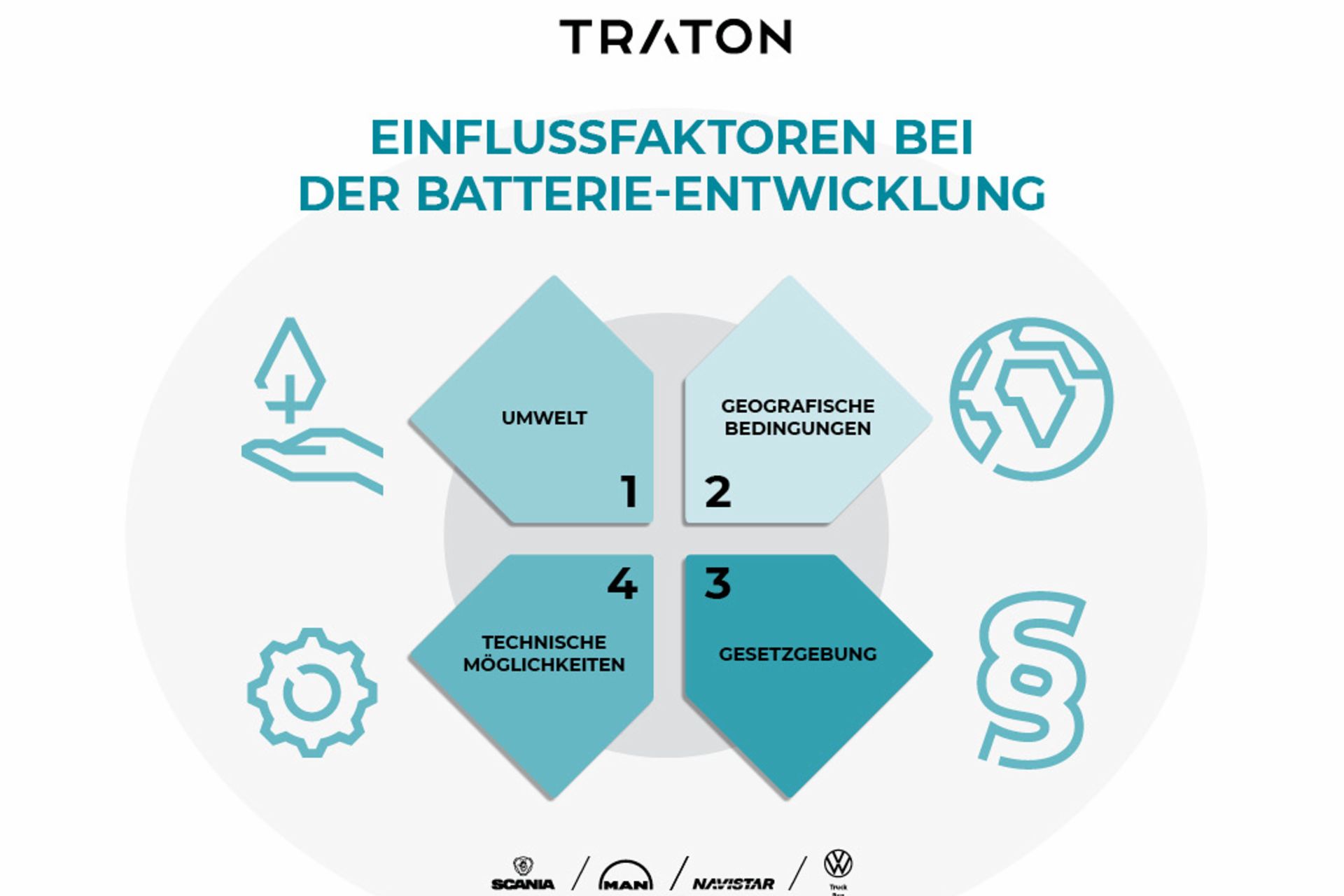
Bis vor Kurzem lag das Hauptaugenmerk der batterieelektrischen Revolution auf Personenkraftwagen. Nun aber erweitert sich der Fokus auf Nutzfahrzeuge, die unterschiedliche Anforderungen erfüllen müssen, wie die effiziente Verteilung von Gütern oder Personen auf lokaler Ebene und den Langstreckentransport.
Für kommerzielle BEVs müssen verschiedene Aspekte neu bewertet werden. So müssen ihre Batterien eine ausreichende Reichweite bieten. Darüber hinaus müssen die Lebensdauerkosten und das Gewicht dieser Fahrzeuge sorgfältig bewertet werden, da sich diese Faktoren direkt auf die Rentabilität und Nachhaltigkeit der Logistik- und Transportvorgänge der Fahrzeugkunden auswirken können. Hinzu kommt, dass die Nachfrage nach Batterien rasch zunimmt, da die Transportindustrie erhebliche Fortschritte bei der Elektrifizierung macht, was schnell wachsende Produktionskapazitäten erfordert.
Ein weiterer zu berücksichtigender Faktor ist die Umsetzung strenger Emissionsvorschriften (und Anreize), die von Regierungen in aller Welt eingeführt werden, um den Übergang zur CO2-Neutralität voranzutreiben. Dazu gehören Emissionsgrenzwerte sowie eine Reihe von Sicherheitsstandards und Recyclingrichtlinien, die von Land zu Land sehr unterschiedlich sein können. So hat die Europäische Union beispielsweise eine Reihe von Vorschlägen und Vorschriften angekündigt (u. a. ist die EU-Battery-Regulation am 18.08.2023 in Kraft getreten), um ihr rechtlich verbindliches Netto-Null-Ziel bis 2050 zu erreichen. Und in Nordamerika haben Politiker gemeinsam mit den großen Automobilherstellern harmonisierte Standards für Treibhausgasemissionen und den Kraftstoffverbrauch festgelegt. Bis 2030 müssen in den Vereinigten Staaten 50 % der neuen Pkw und leichten Nutzfahrzeuge emissionsfrei sein. Ähnliche Standards werden für mittelschwere und schwere Nutzfahrzeuge angestrebt, mit dem Ziel, die Stickoxidemissionen (NOx) zu reduzieren.
In diesem Wissen machen TRATON und seine Marken bereits jetzt große Fortschritte bei der Sicherung strategischer Partnerschaften mit Batterieanbietern. Im April stellten Scania und Northvolt eine gemeinsam entwickelte Batteriezelle für schwere BEVs vor. In Validierungstests hat die Lithium-Ionen-Zelle bewiesen, dass sie einen Lkw 1,5 Millionen Kilometer lang mit Strom versorgen kann – das entspricht der gesamten Lebensdauer des Fahrzeugs. Die Zelle wird mit grünem Strom in Nordschweden hergestellt und hat einen CO2-Fußabdruck, der etwa ein Drittel desjenigen vergleichbarer Batterien in der Branche beträgt.
Anwendungsfälle für kommerzielle BEVs: städtischer Vertrieb und Langstreckenanwendungen
Der Aspekt, der sich am stärksten auf die Batterieanforderungen auswirkt, sind die unterschiedlichen Einsatzbereiche von schweren BEVs. Die meisten von ihnen fallen in zwei Hauptkategorien: Langstreckenverkehr und städtischer Verteilerverkehr. Diese Anwendungen haben eine hohe Jahresfahrleistung und damit einen Produktlebenszyklus von mehr als einer Million Kilometer und erfordern sehr individuelle Spezifikationen. Diese Unterschiede machen jedoch kein völlig neues Zellendesign erforderlich. Vielmehr sind maßgeschneiderte mechanische und chemische Optimierungen erforderlich, um den unterschiedlichen Nutzungsmustern und Lebenszyklen von Lkw und Bussen gerecht zu werden.
Lange Zeit gab es Befürchtungen, dass schwere Nutzfahrzeuge im Fernverkehr aufgrund der langen Strecken, die sie zurücklegen, und der hohen Kosten für ihre Batterien nicht elektrifiziert werden könnten. Diese Annahme wurde bereits entkräftet: Diese Fahrzeuge legen enorme Strecken auf den Autobahnen zurück; im Durchschnitt fährt ein Fernverkehrs-Lkw zwischen 130.000 und 160.000 Kilometer pro Jahr (bei durchschnittlich 520 Kilometern an 250 Tagen pro Jahr). Daher haben gewerbliche Langstrecken-BEVs eine höhere Anzahl von Ladezyklen und einen höheren Energiedurchsatz pro Zelle im Vergleich zu Pkw, die in der Regel für eine Fahrleistung von rund 240.000 Kilometern während ihrer gesamten Lebensdauer ausgelegt sind.
Die erforderlichen größeren Reichweiten beeinflussen sowohl die Batterien als auch die Art und Weise, wie sie geladen werden. Langfristig werden diese größeren Fahrzeuge dem Megawatt Charging Standard (MCS) entsprechen, der derzeit entwickelt wird, um höhere Ladeleistungen zu erreichen. Der MCS arbeitet mit bis zu einem Megawatt, was bei der Größe der Batterien einer C-Rate von etwa 1,2 – 1,4 entspricht (C-Rate 1 ist der Strom, der benötigt wird, um eine Batterie in einer Stunde zu laden) und führt trotz der hohen Systemleistung zu einem relativ sanfteren Ladevorgang, der die einzelnen Batteriezellen weniger belastet. Im Gegensatz dazu bietet das standardmäßige kombinierte Ladesystem (Combined Charging System, CCS) für Personenkraftwagen schnellere Ladegeschwindigkeiten und erreicht etwa 350 Kilowattstunden (kWh), arbeitet aber mit einer höheren C-Rate (kleines Batteriesystem) von etwa 3 – 4 im Vergleich zu kleineren Batterien in einem Pkw. Das bedeutet, dass CCS zwar eine schnellere Aufladung ermöglicht, aber die Batteriezellen im Vergleich zu MCS (bei großen Batteriesystemen) stärker belastet werden. Letztendlich führt dies zu einer längeren Lebensdauer des Fahrzeugs. Darüber hinaus bietet die bestehende Batteriechemie noch erhebliches Potenzial. Es wird erwartet, dass Langstrecken-BEVs in der Zukunft in der Lage sein werden, mit einer Ladung weit über die schon geplanten 500 Kilometer zu kommen, selbst unter schwierigen Umweltbedingungen.
Bei Verteilerfahrzeugen wie Last-Mile-Lieferwagen und Stadtbussen, die in erster Linie über kürzere Entfernungen in innerstädtischen Verkehr unterwegs sind und häufig angehalten und gestartet werden müssen, sehen die Anwendungsfälle ganz anders aus. Diese Fahrzeuge legen in der Regel rund 65.000 Kilometer pro Jahr zurück (das entspricht etwa 300 Kilometern pro Tag an bis zu 365 Tagen im Jahr). Sie haben eine tägliche Betriebszeit von bis zu 20 Stunden (gerechnet mit 100 – 500 Stopps pro 100 Kilometer). Lieferwagen können in der Regel tagsüber aufgeladen werden, wenn die Waren auf dem Betriebshof be- und entladen werden. Die strategische Installation von Schnellladestationen kann deshalb eine effiziente Aufladung gewährleisten. Last-Mile-Lieferwagen, wie der MAN eTGE, werden von Kurierdiensten für den Transport von Paketen und Päckchen innerhalb von Städten eingesetzt. Batterieelektrisch angetriebene Stadtbusse dienen derweil dem öffentlichen Nahverkehr für Einheimische und Touristen. Diese Fahrzeuge legen nicht so weite Strecken zurück wie Lieferfahrzeuge, müssen nicht den ganzen Tag über aufgeladen werden und können bei ihrer Rückkehr zum Busbahnhof über Nacht zu kostengünstigen Tarifen Strom tanken.
Die Batteriekapazitäten dieser Fahrzeuge müssen eine ausreichende Reichweite für die täglichen Fahrten bieten und gleichzeitig häufiges Auf- oder Gelegenheitsladen ermöglichen. Da ultralange Reichweiten jedoch nicht unbedingt erforderlich sind, können die Batteriegrößen dieser Fahrzeuge im Hinblick auf geringere Gewichte und Kosten optimiert werden. Dies gibt den Kunden die Freiheit, die Batterieparameter so zu wählen, wie sie ihr jeweiliges Fahrzeug nutzen wollen.
Ein modularer Batterieaufbau ist die richtige Lösung für alle Marken der TRATON GROUP
Angesichts der Notwendigkeit, die ökologischen und mechanischen Anforderungen von BEVs sowohl für den Fern- als auch für den Verteilerverkehr zu erfüllen und gleichzeitig den spezifischen regionalen Anforderungen und global unterschiedlichen Normen gerecht zu werden, hat sich eine entscheidende Komponente herauskristallisiert, um diese Herausforderung zu meistern: anpassungsfähige Batteriekonzepte. Anpassungsfähige Batterien können auf den spezifischen Energiebedarf und die Gewichtsbeschränkungen jedes Fahrzeugtyps zugeschnitten werden, um die Reichweite und die Leistungsmerkmale zu optimieren.
In seiner Funktion als Head of Technology Strategy & Innovation in der TRATON GROUP ist Dr. Götz von Esebeck davon überzeugt, dass die anpassungsfähige Batterietechnologie einer modularen Plattform den Nutzfahrzeugherstellern die Flexibilität bietet, Fahrzeuge zu entwickeln, die in mehreren Märkten verkauft werden können. „Für unsere Kunden ist ein Nutzfahrzeug eine Investition, die sich erst dann auszahlt, wenn es im Einsatz ist und fährt. Deshalb müssen wir sicherstellen, dass unsere Batterien diesen Anforderungen gerecht werden und gleichzeitig dafür sorgen, dass wir auf Marktstörungen und lokale Lieferengpässe vorbereitet sind. Wenn unsere Batterietechnologie in Zukunft standardisiert ist, können wir leichter auf Marktstörungen reagieren.“
„Für unsere Kunden ist ein Nutzfahrzeug eine Investition, die sich erst dann auszahlt, wenn es im Einsatz ist und fährt. Deshalb müssen wir sicherstellen, dass unsere Batterien diesen Anforderungen gerecht werden, und gleichzeitig dafür sorgen, dass wir auf Marktstörungen und lokale Lieferengpässe vorbereitet sind.“
Dr. Götz von Esebeck, Head of Technology Strategy & Innovation bei der TRATON GROUP
Die Entwicklung und Erprobung neuer Batterietechnologien kann teuer und zeitaufwendig sein. An die Plattform angepasste Batteriedesigns, die für verschiedene Fahrzeugmodelle wiederverwendet werden können, senken die Gesamtkosten für Forschung und Entwicklung.
Die TRATON GROUP, die über ein vielfältiges Produktportfolio verfügt, arbeitet daran, gemeinsame Batterien herzustellen, die weltweit für alle Marken und Fahrzeuge eingesetzt werden können. Grundlage dafür ist die Entwicklung eines konzernweiten TRATON-Baukastensystems, das standardisierte Schnittstellen für die wichtigsten Technologiebereiche bietet.
Um die grundlegenden Spezifikationen für gängige Batterien und Komponenten wie Zellen und Module festzulegen, führt TRATON eine umfassende globale Anwendungsfallanalyse für kommerzielle BEVs auf der ganzen Welt durch. Zusätzlich zu den lokalen Vorschriften und Lieferkettenfaktoren berücksichtigt dieser Ansatz sowohl Umweltfaktoren als auch mechanische Faktoren. So müssen beispielsweise je nach Einsatzort unterschiedliche klimatische und thermische Bedingungen berücksichtigt werden. In Schweden beispielsweise müssen die Batterien auch bei extrem niedrigen Temperaturen zuverlässig funktionieren, was den Wirkungsgrad und die Reichweite der Batterien verringern kann. In wärmeren Ländern wie Spanien hingegen müssen die Batterien mit höheren Temperaturen zurechtkommen, da übermäßige Hitze ihre Degradation beschleunigen kann.
Die Auswirkungen extremer Umgebungsbedingungen lassen sich durch fortschrittliche Kühl- und Heizsysteme effizient bewältigen. Diese Systeme sorgen für eine optimale Leistung und Haltbarkeit, sowohl bei häufigen Ladezyklen für Verteilerfahrzeuge als auch für Langstrecken-Lkw, bei denen die Batterien über lange Strecken stabile Betriebstemperaturen gewährleisten müssen, um funktionsfähig zu bleiben und eine optimale Leistung zu erbringen. (Hier wurde der letzte Satz gestrichen).
Auch mechanische Faktoren wie Stöße und Vibrationen müssen bewertet werden. In Südamerika sind robuste Akkupacks für unwegsames Gelände unerlässlich. Unebene Straßenoberflächen können Fahrzeuge ständigen dynamischen Kräften aussetzen, die Batterie- und Aufhängungssysteme beeinträchtigen können. Deshalb ist es von entscheidender Bedeutung, dass robuste Aufhängungssysteme, die mit Techniken zur Schwingungsisolierung und Komponentenverstärkung ausgestattet sind, zusammen mit fortschrittlichen Testverfahren eingesetzt werden, um die Batterien vor nachteiligen Auswirkungen zu schützen und ihre Zuverlässigkeit, Langlebigkeit und allgemeine Betriebseffizienz sicherzustellen.
Jeder Markt unterliegt auch regionsspezifischen Bedingungen, wie beispielsweise marktspezifischen Anschlüssen, die bei der Konstruktion von Lkw berücksichtigt werden müssen, um eine nahtlose Kompatibilität und einen effizienten Betrieb in verschiedenen Gebieten zu gewährleisten.
Die gemeinsame Batterielösung von TRATON ermöglicht Synergien und Skalierbarkeit
Als Produktmanager für Batterien in der TRATON GROUP erlebt Dr. Stefan Tillmann aus erster Hand, wie die gemeinsame Lösung des Unternehmens mit einem modularen System Synergien und Skalierbarkeit möglich macht. „Bei TRATON entwickeln wir Komponenten, die weltweit und markenübergreifend eingesetzt werden können. Dieser strategische Ansatz rationalisiert nicht nur Entwicklung, Tests, Freigabe und Aftermarket-Support für uns als Gruppe, sondern erhöht auch unsere Widerstandsfähigkeit gegenüber Marktverwerfungen. Darüber hinaus bedeutet die Verwendung gemeinsamer Komponenten eine Senkung der Gesamtbetriebskosten für unsere Kunden.“
„Bei TRATON entwickeln wir Komponenten, die weltweit und markenübergreifend eingesetzt werden können. Dieser strategische Ansatz rationalisiert nicht nur Entwicklung, Tests, Freigabe und Aftermarket-Support für uns als Gruppe, sondern erhöht auch unsere Widerstandsfähigkeit gegenüber Marktverwerfungen.“
Dr. Stefan Tillmann, Product Manager Batteries bei der TRATON GROUP