The new common base engine from the TRATON GROUP is better for the environment than comparable diesel engines and represents a sustainable transition into the world of battery electric transportation. At the same time, the engine drives collaboration between the TRATON brands — in terms of production, global procurement, and IT infrastructure.
There’s no question about it: electric trucks and buses will be the foundation of a climate-neutral world of transportation. Even today, they make an important contribution in many applications. The TRATON GROUP, too, is already seeing its first battery electric trucks and buses roll off the production line, while at the same time developing its first autonomous trucks. However, it will be some time before the entire product portfolio is electric, since in many areas of application, the requirements — such as a powerful charging infrastructure — are still in the implementation phase. In order to bridge the time until these requirements are met, engineers in the TRATON GROUP have developed a new engine, the common base engine (CBE) — TRATON’s last generation of diesel engines. Compared to traditional diesel engines, the CBE consumes significantly less fuel. It also has the lowest CO2 emissions of any engine in the TRATON GROUP.
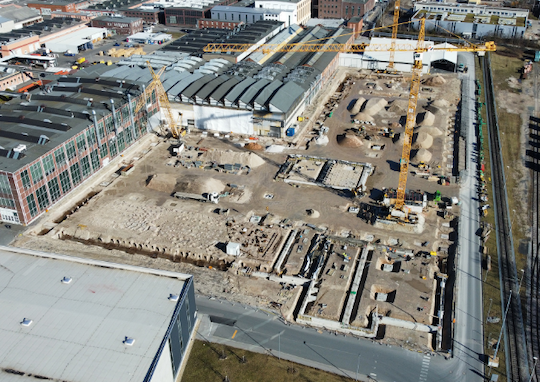
MAN has invested a lot in the Nuremberg site and will be building the CBE in series there from 2024.
In the future, it will be used in heavy-duty commercial vehicles from the Scania, MAN, and Navistar brands, and later also by Volkswagen Truck & Bus.
But why is it still worthwhile to develop a new diesel engine given the transition to battery electric drives? “The future — of mobility and not just of TRATON — is electric,” says Michael Tzomakas, at that time in his role as Head of the Future Powertrain Program at MAN in Nuremberg in June 2022. Still, it will be years before electric mobility is a feasible option across the board — this may even take decades in some regions. “Until then, we have a transitional solution in the form of the CBE, which is even more efficient and better for the environment than previous diesel engines.”
The CBE is not just a conclusion, but a high point: the brands Scania, MAN, and Navistar worked closely together on its development — particularly in the areas of production, purchasing, and IT infrastructure. They developed the new product and tested it together as a team, working virtually due to the COVID-19 pandemic.
IT infrastructure: synchronizing the brands
Mathey Wiesbeck, Head of Processes and Methods in the Group Product Management of the TRATON GROUP in Södertälje, is responsible for synchronizing the brands involved in the product development processes of the CBE project. This is due to the need for a shared approach, a uniform method, to describe the processes within the project, the brands’ different operating systems. Wiesbeck explains: “Our collaboration models define which brand takes the lead in the development project, what tasks and responsibilities are involved, and what the other brands need to supply for this project.” Scania is the lead brand for the CBE and guides the other brands. The collaboration models also set all the important information on the funds, resources, problem-solving, and intellectual property.
The CHAMP platform plays an important role in the dialogue between the brands by ensuring that data from one brand can be used in the systems of the others. The brands have different ways of defining components and products in their respective IT infrastructures. The exchange of this information via CHAMP ensures that all brands can use each component as though they had developed it themselves. To this end, things like drawings, drawing numbers, and critical parts master data need to be transferred. If there is new information on a topic, it is essential for all project partners to receive it.
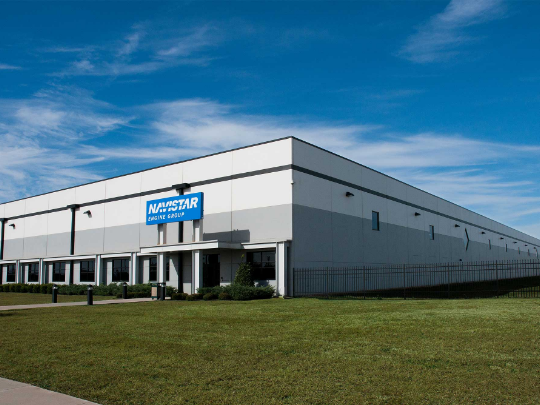
Navistar will produce the CBE in Huntsville, USA, starting in 2023.
This is a long, manual process that cannot be completed overnight. “The development took place mainly on Scania platforms,” says Wiesbeck. “But the product, the CBE, also has to be available in the systems of Navistar and MAN — as if it were these brands’ own product.” Change management and failure management processes also need to be mapped between the brands. “This is particularly relevant for the period in which the product is actually in operation,” says Wiesbeck. To this end, the CHAMP platform also regulates escalation mechanisms and governance structures. Wiesbeck is convinced: “The requirements of the CBE triggered developments in the platforms and processes that offer a strong basis for collaboration in the future.” The goal is to one day have a joint infrastructure for data that will increase efficiency. "We will move from synchronisation to communalization", explains Wiesbeck. All the brands in the TRATON GROUP would then be able to access all data on an equal footing — which will also be very important in future projects in electric mobility and autonomous driving. “The CBE will be the base solution for our future autonomous vehicles,” confirms Ryan Ludera, Senior Program Manager at Navistar. He says that as soon as the CBE is in operation, customer data will be collected in order to obtain a better usage profile and carry out any adjustments. “We also want to understand the effects of things like different speeds or degrees of efficiency on the engine and on fuel consumption. That way, we can make future variants of the CBE even more efficient and ultimately come up with an even better product.”
Production and procurement: reduced consumption, fewer emissions
At Scania, the CBE has been in production since 2022. It will be produced at Navistar from 2023, the company introduced its version of the CBE, the International S13 Integrated Powertrain, in August 2022. MAN will follow suit with series production in 2024. It is planned that Volkswagen Truck & Bus will use the CBE from 2028. The brands have each invested a large sum of money in their sites. The CBE engines will not be produced in a central factory, but instead at various locations — the engines for Scania will be made in Södertälje, Sweden, those for MAN in Nuremberg, Germany, the engines for Navistar in Huntsville, Alabama, USA, and the engines for Volkswagen Truck & Bus in São Bernado de Campo in Brazil, where also engines and gearboxes for Scania Latin America will be produced. “To avoid differences in quality between the engines, we are procuring tools, machines, and components together and have also standardized the production process,” explains MAN’s Michael Tzomakas. “This way, we can ensure the same quality at every site around the world.”
In Södertälje, Scania has built a new foundry for the engine’s crankcase and is delivering cast parts to MAN in Nuremberg. Not only does this approach bring cost benefits, it also offers the individual production sites a certain degree of flexibility: if a factory has a bottleneck in a certain area, another factory can readily help out with components and similar parts. With the joint powertrain, there is a global supplier basis for trucks and buses, and an opportunity to spread capacities between the four engine factories in Södertälje, Nuremberg, Huntsville, and São Bernado de Campo. Tzomakas also sees this close collaboration between the brands as a positive — and not just because of global procurement: “With this cooperation, the workload is spread among more people, which is a great advantage. We’ve learned a lot from this joint project. I am certain that all the brands will be able to advance significantly with the CBE,” says Tzomakas.
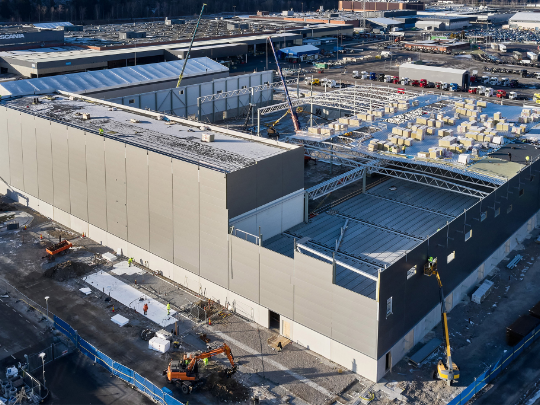
Scania has also invested heavily in its Södertälje production site – among other things, the Swedes have built a foundry.
Learning together
But it’s not just the product itself that’s a first; the Group-wide collaboration on such a project also marks a turning point in the history of the TRATON GROUP: “It is the first cross-brand collaboration on this scale,” says Tzomakas. Robert Dubois, Head of the Production Network and Strategy department in the TRATON GROUP, agrees. He says: “We’ve learned a lot in this joint project for future collaboration. We used it to set standards in terms of things like working processes and procurement. Regardless of whether we produce components in Huntsville, Nuremberg, or Södertälje, the methods and tools we use are always the same.”
Beyond that, the employees of the various brands have also grown closer together as a result of this collaboration. “The project has strengthened our team spirit and helped us to advance as a Group. We now feel well-equipped to take on future challenges,” says Dubois. Darren Gosbee, Vice President of Engineering in research and development at Navistar in Lisle, Illinois, sees things similarly: “The collaboration has helped us to better understand not just each other, but also the respective markets of the TRATON GROUP. The result is a new form of trust between us all.”
The path is open
The CBE project isn’t just cross-brand and cross-department, it is also an intercultural project in which people from Germany, Sweden, the US, and many other countries work together. “The working language of the project staff is English. The collaboration is going really well; we have grown closer and closer together as time has gone on,” says Ludera, though he admits that there are naturally challenges from time to time. “You always have to be aware of the differences in culture and company culture.” His Swedish colleague Karin Elfgren, who works together with Ulf Angsmyr as an Senior Project Manager at Scania and adapts the respective software systems together with him, adds: “We try to understand what is considered important in each culture. Being aware of cultural idiosyncrasies helps us avoid misunderstandings and build trust between employees.”“In the coming years, the brands will work more and more intensively with each other,” says Angsmyr, Senior Project Manager at Scania. “This is our goal at TRATON.” He believes the CBE project has helped the employees of the different brands and in the areas of production, procurement, and IT to grow together and build up trust. And he is convinced: “If we are smart about the use of our resources, help each other, and are prepared to learn from each other, we will also continue to be successful in the long term.” Although things were not always easy, the team has proven that together, it is capable of successfully mastering such complex joint projects. With that, the path to future Group-wide projects is now open.