Modularization is rooted in principles of efficiency and adaptability. It involves introducing a component series with standardized interfaces for a given function and adjusting performance steps within an existing component series while maintaining these interfaces and evaluating the series comprehensively. The strength of modularization lies in optimizing performance steps to precisely meet customer needs, a crucial distinction from relying on standard components from suppliers or aiming solely for a reduced total number of parts.
From a product standpoint, the overlap between passenger cars and commercial vehicles is surprisingly small – so much so that Volkswagen Group has opted against developing a single Group-wide modular solution. Compared to passenger vehicles, the number of customization possibilities for commercial vehicles is substantially higher.
The key differences between passenger cars and commercial vehicles
So, what are the key differences between passenger cars and commercial vehicles? Designed for the mass market, passenger cars are sold in high volumes; for a major automaker, a key model may sell around one million units per year, compared to 100,000 truck units sold annually. Additionally, passenger cars must support multiple models and variants, as car manufacturers are required to respond quickly to changing market trends and consumer preferences. With a focus on personal transportation, comfort and the driving experience, their designs typically offer fewer customization options compared to commercial vehicles. Due to these factors, passenger cars necessitate standardization and modular platforms to achieve economies of scale, while also accelerating the time-to-market for new models by harmonizing the development process.
Conversely, commercial vehicles are primarily designed for utility and must deliver a specific level of performance to support income-generating applications. Therefore, their level of modularity must be far higher. In contrast to passenger cars, which tend to be driven up to one hour out of every 24, uptime is extremely important for commercial vehicles as they must generate income for their owners. Commercial vehicles drive more than 300,000 kilometers per year, with some trucks only stopping the engine at the service station. By contrast, the average passenger car drives 15,000 to 30,000 kilometers per year.
Through modularization, the use of standardized interfaces and well-balanced performance steps, manufacturers can offer a wide array of highly customizable and tailored solutions to meet the specific needs of customers operating in different regions and industries, from logistics to construction. Understanding where performance needs overlap allows for component re-use, achieving significant economies of scale while supporting an extremely high level of customization.
The TRATON GROUP utilizes its own TRATON Modular System (TMS) to translate the requirements of its customers into technical solutions by identifying clusters of needs that can be met with the right solutions. “From a technological perspective, the heart of the TRATON Modular System is translating customer requirements into technical solutions using a sophisticated user-factor methodology and prioritizing the standardization of interfaces,” says Martin Björklund, Product Strategy Modularization, in the TRATON GROUP.
Design flexibility, customization and technical requirements
When it comes to design and technical requirements, passenger cars are tailored to general consumer preferences by aggregating an average of 12-15 different customer personas, whereas commercial vehicles are designed to meet specific commercial demands.
When making their purchasing decisions, passenger car consumers weigh up a variety of factors, including aesthetics, comfort, infotainment systems, and driving performance. Additionally, powertrain efficiency can be enhanced by tailoring it to suit consumer driving preferences.
Besides the requirements regarding the durability and uptime of commercial vehicles, advanced technologies like telematics, autonomous driving aids, and connectivity solutions tailored to fleet management and logistics need to be seamlessly integrated. This modular approach, seen in the TMS, enables manufacturers to easily adapt a vehicle’s configuration to different use cases by employing scalable powertrains, reinforced chassis for various load types and life cycle requirements, and specialized equipment installations. Adaptable cargo spaces can be customized to meet diverse technical specifications, ensuring each vehicle perfectly suits its intended operational environment.
Battery placement and management
Additionally, for battery electric vehicles (BEVs), effective battery placement and management are pivotal to optimizing performance and efficiency.
In BEV passenger cars, the placement and management of batteries is crucial for optimizing space efficiency, weight distribution, and driving dynamics. Automakers strategically position batteries to lower the center of gravity, enhancing vehicle stability and handling. This careful placement also maximizes interior space to enhance comfort and practicality for occupants. Modular battery packs allow for varying ranges and power outputs, catering to different driving preferences.
For commercial BEVs, battery placement and management take on different priorities. The modular design of batteries in this segment enables easy scalability to meet various composition requirements, such as wheel configurations (e.g. extra front axles, tandem drive axles, eight wheelers, auxiliary equipment) and facilitates straightforward maintenance and replacement. Batteries are installed in the vehicle to maximize cargo space or range, maintain overall vehicle stability, or, in the case of industrial BEVs, to make space for large components like cranes or garbage compactors. Typically, batteries are placed along the side of the chassis, within the frame, or on the roof of buses, depending on use and where space is needed for cargo.
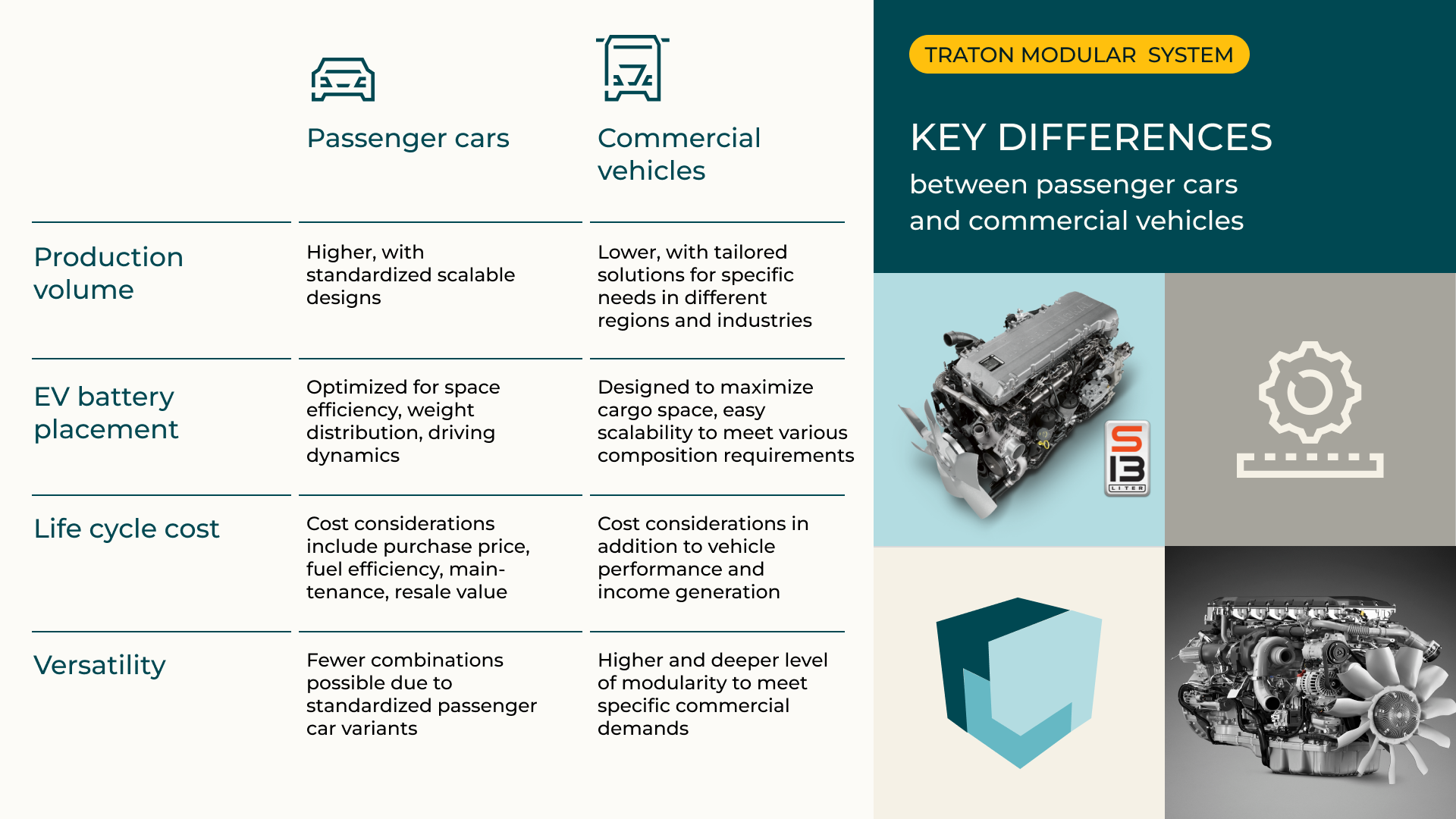
Life cycle costs
For both vehicle types, cost considerations play a significant role in their design and management. This impacts everything from initial purchase decisions to long-term operational efficiency and value retention. In the realm of commercial vehicles, the focus is on Total Operational Economy (TOE), in addition to Total Cost of Ownership (TCO), which emphasizes vehicle performance as it relates to income generation. This makes tailoring vehicles to specific use cases even more imperative. The initial purchase price must remain competitive, while maintenance costs, fuel efficiency, operational downtime, and robust after-sales support remain important considerations.
It is essential that commercial vehicles can be continuously improved throughout their life cycles, with components potentially re-used in subsequent ‘second life’ applications after their initial use. Modularization supports these demands by promoting incremental upgrades over complete redesigns. Modular components such as engines, transmission systems, and axles can be quickly replaced or upgraded to extend a vehicle’s lifespan and reduce service time owing to the use of standardized interfaces. This approach is vital for maintaining fleet efficiency and reliability. Meanwhile, modular components allow fleets to keep up with technological advancements and remain compliant with evolving regulations.
Modularization is a transformative approach
In essence, modularization in the transportation industry is a transformative approach that addresses the diverse and evolving needs of both passenger cars and commercial vehicles. While both vehicle types share common factors such as connectivity and electrification, their approaches to modularization differ significantly due to their unique operational requirements and market demands.
Passenger cars prioritize standardization to achieve economies of scale within their platform, expedite time-to-market, and offer a variety of customizable features to enhance the consumer experience. On the other hand, commercial vehicles emphasize a higher and deeper level of modularity to support extensive customization, durability, and operational efficiency. These factors are crucial for their utility-focused applications and extended usage.
Through modularization, the TRATON GROUP achieves economies of scale at a lower component level by enabling component reuse across its brands throughout their entire product ranges. Organizations like TRATON serve as prime examples of successful modular strategy implementation, translating customer needs into technical solutions and driving innovation through open combinatorics.
As the transportation industry continues to evolve, modularization will remain a key enabler of efficiency, adaptability, and sustainability, ensuring that commercial vehicles can effectively meet the challenges of the future.