Scania’s success is partially due to a particular approach taken during the development and production of commercial vehicles. The “Byggladan principle,” which is derived from the Swedish word for “modular toolbox,” is based on using as many common parts as possible to produce a wide range of customer-specific variants.
At first, it all sounds very simple. Take an engine, transmission system, axles, chassis, frame, and finally the cab: a truck is made up of relatively few, large modules. Put standardized interfaces on these modules, and they are easily interchangeable. This allows for the production of many different vehicles from only a few systems. That basically sums up the “Byggladan principle,” Scania’s modular toolbox system.
“Our recipe for success is actually not that simple,” says Hans Holmlöv, putting it into perspective. “But modularization does create a win-win situation—for both the customer and Scania. This is because, although we use standardized components, we can offer specific and tailored solutions for each and every intended use of the vehicle.” Holmlöv would know; a mechanical engineer, he’s been working for Scania in Södertälje for 35 years. He knows full well that standardized series production and customer-specific vehicle variants can go hand in hand.
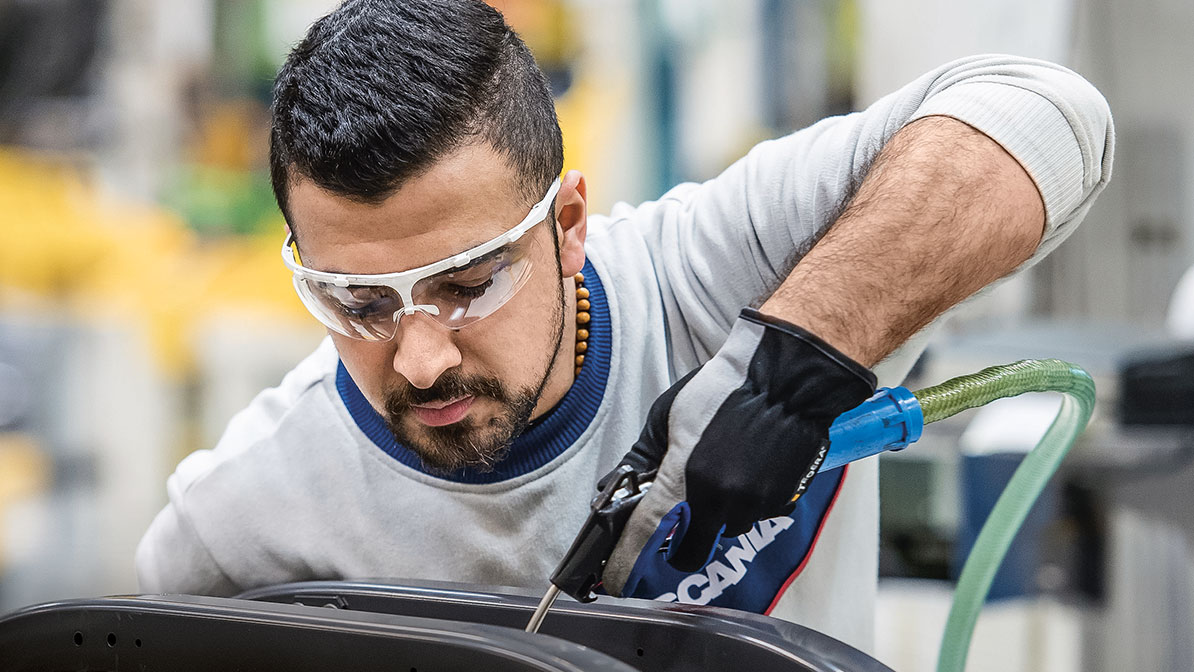
The greatest advantage of the Byggladan principle: for every intended vehicle use, a custom-fit vehicle can be built—regardless of the number of units.
“Millions of different combinations can be built on one assembly line in Södertälje.”Hans Holmlöv
Mechanical engineer, Scania
The greatest advantage of the Byggladan principle is that for every intended vehicle use, a custom-fit vehicle can be built, regardless of the number of units. “Even if a customer only needs one very specific truck, we can assemble it from existing modules,” Holmlöv explains proudly. This gives Scania the capability of producing niche products and short series runs competitively. This includes special-purpose commercial vehicles such as fire department vehicles, winter service vehicles, or specialized construction vehicles. A truck with six axles—four of them powered—combined with a powerful V8 engine, a low chassis, and a small cab: unusual combinations like this one are easy to develop and produce thanks to modularization. Hans Holmlöv hasn’t even begun to work out how many variants are theoretically possible. But one thing is certain: “Millions of different combinations can be built on one assembly line in Södertälje.”
A common parts strategy to save costs
For a premium supplier, it is important to roll out new features and product improvements to the market as quickly as possible. At Scania, this is a continuous process: “Whenever our engineers have developed something new, it can be quickly transferred into series production,” says Holmlöv. Having said that, new features don’t necessarily mean more parts. The previous Scania generation consisted of around 25,000 individual parts, while the current generation has about 22,000. This is a reduction of 11%. At the same time, the number of product variants increased. Another advantage is that through modularization, there is a smaller amount of replacement parts. Scania also applies the common parts strategy to buses. For example, the front steering axle of a tractor can also be built into a bus as a trailing axle. Likewise, with higher volumes for these parts comes a more favorable cost structure. Scania also needs fewer suppliers, whose products can be better controlled. In turn, this guarantees higher product quality.
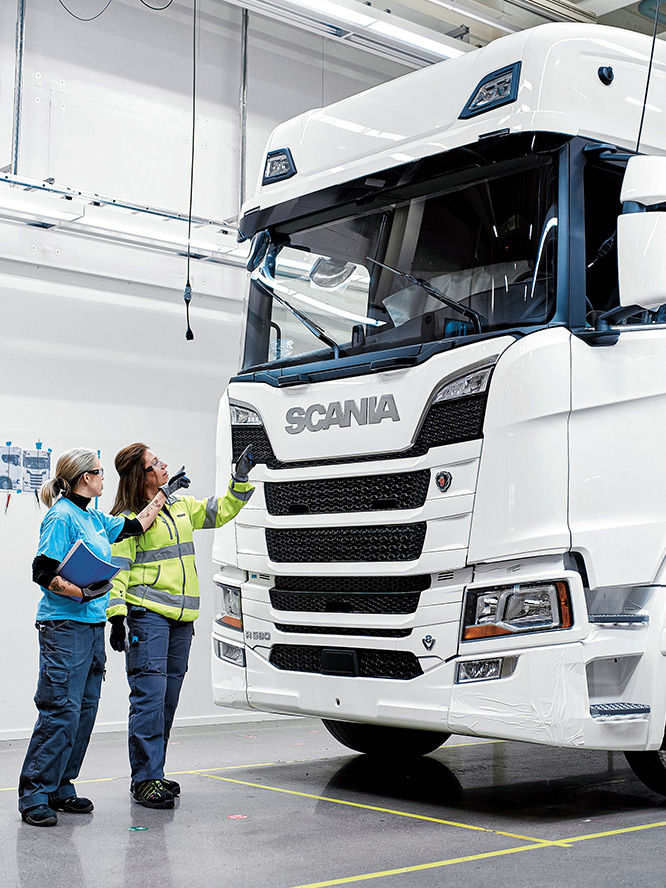
The previous Scania generation consisted of around 25,000 individual parts, while the current generation has about 22,000.
Worthwhile development collaboration
“We are often asked: if the system is so effective, why don’t other manufacturers do the same?” says Holmlöv. This is because it’s not actually that easy. Scania has been employing the Byggladan principle since the 1930s. Back then, the cylinders were the same in all engines. Since the 1980s, Scania has used a fully modularized production system. And over many decades, it has developed and perfected a unique system. A history like that is not so easy to replicate. “Young engineers fresh out of university are all well-versed in CAD systems. But modularization is not often part of the curriculum at universities,” says Holmlöv, who studied mechanical engineering. The modular concept is a real challenge for the engineers. Designing a component that can be used in many commercial vehicle models, and even in both trucks and buses, is quite tricky.
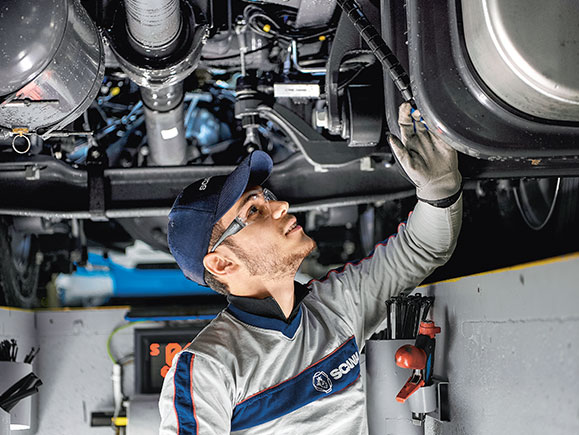
Scania has perfected a unique system over many decades.
Within the TRATON GROUP, there are many reasons not to start from scratch when it comes to pursuing future new developments at Scania and MAN. “The modular way of thinking offers the two companies the perfect opportunity to learn from each other. And both definitely have a wealth of experience,” says Hans Holmlöv. For example, it hardly makes sense to put in enormous effort to develop different axles, transmission systems, and engines for the same application. Collaboration reduces both development and production costs.
With the Common Base Engine 1, MAN and Scania are currently jointly developing an engine platform for heavy-duty commercial vehicles. While customers benefit from a highly efficient engine, the commercial vehicle manufacturers together save a considerable amount in investment and material costs. The engine is set to be used in every second truck by the mid-2020s. Synergies are also realized in the development of the entire powertrain: with its modular design, it has universal application in both trucks and buses.
Hans Holmlöv will see the results of the cross-brand collaboration while still working for Scania. Although at 65 he could already retire, he has chosen to work one, maybe even two, years longer. He’s obviously still captivated by the Byggladan principle.