The commercial vehicle industry and transport fleets are facing enormous challenges when it comes to decarbonizing road transport. Electrified trucks with battery-electric drivetrains, which are now production-ready following extensive practical testing, are part of the solution. What characterizes a truck and bus battery of the future in terms of performance and range?
The truck battery of the future is powerful and enables ranges of up to 500 kilometers. In the case of smaller commercial vehicles, it’s already becoming apparent that battery-electric drivetrains make great economic sense. And regardless of whether it will be purely battery-electric or with hydrogen technology, the battery will be indispensable in the transport sector of the future. Interestingly, however, many players in the transport sector are not yet fully aware of this development. Moreover, there seems to be a widespread view that truck batteries, unlike car batteries, will not become a cheap mass product in the future – on the basis that the performance requirements are simply too demanding.
In low margin industries like logistics, price plays an important role. How can we ensure that high-performance batteries for trucks and buses remain affordable while meeting quality standards?
The more standardized truck batteries become, the more suppliers can bring battery systems to market and offer them to their customers. This interplay of market forces will lead to lower prices and higher quality in the future.
“The more standardized truck batteries become, the more suppliers can bring battery systems to market and offer them to their customers. This interplay of market forces will lead to lower prices and higher quality in the future.”
Claudius Jehle, Founder and CEO of volytica diagnostics GmbH
But it all depends on how a truck battery is driven, how it is used...
Correct. The quality assurance of a battery, the quality acceptance, the wear – all of this depends massively on how it is used. Even factors such as how it is treated when parked can make a difference because a battery continues to degrade even if it is not used. If it is parked in a full state, it degrades much faster than if it is not fully charged. All these factors have an impact on the quality of the battery and, by extension, the value of the fleet – almost 50% of the fleet value is accounted for by a single wearing part! In other words, reducing the total cost of ownership is decisive. Although the purchase price of a battery will take precedence, other metrics like battery lifespan or residual value will receive a growing amount of focus. A high-priced battery that is used for many years can be much more economical than an inexpensive battery that must be replaced after only three years.
Conversely, does this also mean that the transport companies should be supported in how they handle their battery with care?
The owner, the financing provider and any service provider will need to crunch the numbers very carefully while doing everything to ensure optimal battery health outcomes. For example, by using digital tools that support the logistics provider and tell him when the battery needs to be charged or that the battery should not be left fully charged in the depot. And those who follow these suggestions receive cheaper leasing rates, for example. Everything revolves around the value of the battery.
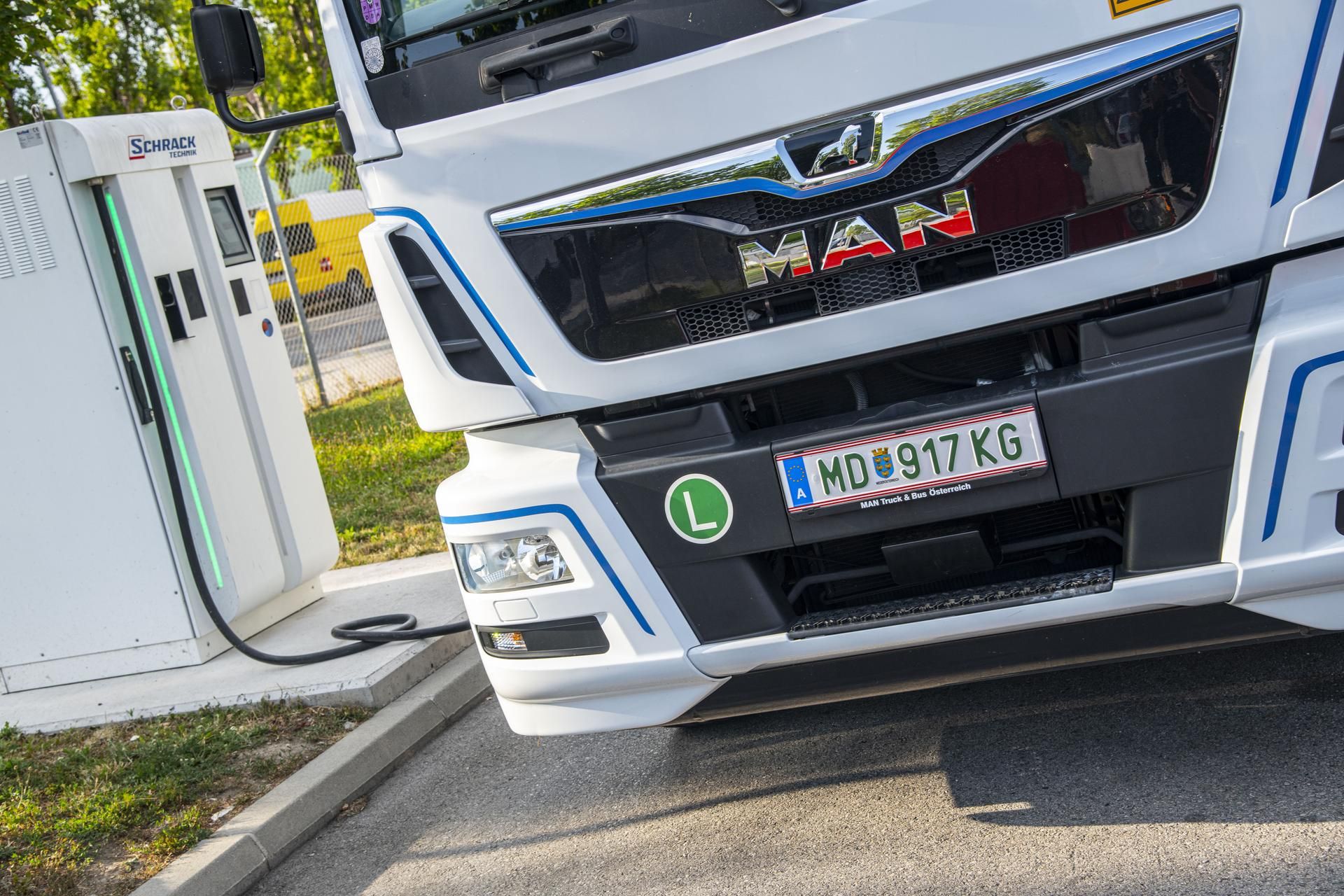
What role will increasing energy density play in the future? And what about increasing efficiency, optimizing use or better state-of-charge determination?
This is a very interesting topic. Increasing the energy density in batteries or battery systems can be achieved in various ways. At the moment, huge sums are being invested to get a few percentage points more range out of batteries by optimizing their chemical composition. To a certain extent, this approach has its limits, especially because the increase in energy density is usually accompanied by a decrease in service life. This predicament is bad for commercial vehicles as battery lifespan is the decisive factor in whether the investment pays off. So, the role of software that controls and monitors the battery will increase in importance. I know of dozens of cases - for example in an e-bus fleet in the Netherlands - where the state of charge of each individual vehicle is misjudged by at least ten percent. So, if we invest many billions of euros to get one, two, three percentage points more energy density into the chemistry, while only being able to assess battery capacity to within a margin for error of 10%, it is not difficult to see why this doesn’t work.
It is becoming increasingly important to know: How much life is still in the battery? How long can I still use it? With the use of these intelligent diagnostic systems, Europe could also score points in the long term. Because very few batteries are actually made in Europe – and those that are tend to be produced by Asian manufacturers. But if we add an intelligent system that improves and realistically estimates the range and performance of a battery, we will have a unique selling point compared to our competitors in Asia.
A central question in the profitability analysis is: When has a battery reached the end of its life? Today, the so-called end-of-life is equated with the end of the warranty. This narrow view leads to the premature discarding of countless batteries that are still fully functional. It’s like yoghurts or a tin can: there is a best-before date on it and not a maximum shelf life. We can assume that 0% of batteries are designed to fail before the end of this warranty period, which means that all batteries that are at the end of their first warranty life must not be ‘ready for scrap’. With good use, batteries can live almost twice as long as the stated end of warranty. So, a battery can and should be used even after the warranty ends. And if it then no longer meets my requirements, I can at least look for a possible buyer for a second use – and prove with a certificate how it was used and in which second-life applications it can potentially still be used.
As buffer storage for solar and wind power systems or, for example, as mobile energy storage for events?
Exactly. It’s up to manufacturers, recyclers and owners to handle the expensive and valuable asset that is the battery with great care. And I expect vehicle manufacturers to be willing to cooperate. Of course, it is a big task to get the owner to think and act so responsibly, and there is a strong case for having a third-party undertake this work on their behalf.
“The longer the battery remains in an optimal state of health, the more economical it is for the vehicle owner, whether that be a leasing company or the vehicle/truck as a service provider.”
Claudius Jehle, Founder and CEO of volytica diagnostics GmbH
Permanent and systematic monitoring, as well as strategic service life optimization, extend the life cycle of a battery for trucks and buses. What skills are needed for this and how can these be built up more comprehensively?
It would be best if owners understand their battery or transfer this task to a service provider who takes over fleet management. Vehicles are becoming more and more networked, classic diesel trucks already communicate their maintenance intervals into the fleet management and asset management systems. So, this is the point where the owner of an e-truck needs to get an answer to his questions about battery quality.
For e-trucks and e-buses to be able to operate in a climate-friendly way, they need electricity. What else is needed besides the development of charging infrastructure?
The expansion of a nationwide supply of infrastructure for e-vehicles is lagging behind the expansion targets. Here, we have the classic chicken-and-egg problem: no one will buy e-trucks as long as there is no high-performance supply infrastructure. And no one builds the infrastructure as long as there are no users. A small solution to the problem could be innovative local logistics hubs for decentralized energy generation with used batteries as buffer storage in places that are distributed across a city, for example, and can have a big impact locally.
Basically, we need more understanding for the battery issue in this country. We have noticed that there is very little widespread understanding about this topic. That is not an accusation: after all, it is a very complex and relatively new topic. Consequently, more knowledge is needed on this subject. And manufacturers should be obliged to share information about the batteries used and their data signals with other stakeholders. Otherwise, users will not be able to take good care of their battery.
What other levers do you see as necessary to electrify commercial vehicle transport?
We need to promote a broader understanding of the challenges and opportunities that come with the technology. There also needs to be a shift away from statements that a battery can only be used for a given length of time. The whole debate would benefit from a healthy dose of pragmatism, particularly regarding questions like how and where the e-truck or e-bus is used on a daily basis. We also need to engage more with drivers and learn more about their personal experiences. I have not met a single driver who is not enthusiastic about battery-electric driving.
Looking into the future, when will people and goods be transported across Europe in a completely carbon-neutral manner, powered by battery technology?
I couldn’t possibly make a prediction on this. But I hope to be able to live to see it, and I am very confident that I will.