Modularity and Group-wide platforms are key factors in the future success of TRATON. And a diesel, of all engines, provides an outlook of how electric drive systems can be jointly developed and produced: the new 13-liter common base engine is the last combustion engine of the TRATON GROUP and, at the same time, the first drive system that arose as a result of cross-brand collaboration.
The fundamental principle of modularity is quite simple: manufacturers design their products in such a way that they can be assembled from modules according to customers’ individual needs. The use of these modules makes development simpler and also reduces production costs. Swedish company Scania has been making the most of this advantage for nearly a century now, and moved entirely to a modular platform system around 40 years ago. The “byggladan principle,” derived from the Swedish word for “construction kit,” also played a significant role in the development of the common base engine (CBE) from the very beginning.
The CBE is the new 13-liter diesel engine of the TRATON GROUP. It will be used in heavy-duty trucks and buses in Europe, North and South America, and possibly in China. And it will also be manufactured where it will be used: by Scania in Sweden and Brazil, Volkswagen Truck & Bus will use the engine in its vehicles. Navistar will produce the CBE in the United States and MAN in Germany. Thanks to the modular platform principle, 80 percent of the engine is the same wherever you go. The remaining 20 percent is made up of components the brands can use to adapt the CBE to the particular requirements of the customers in their respective markets. These could be, for instance, statutory requirements for emission values, which can vary from country to country.
„The new engine was all about reducing fuel consumption and CO2 emissions.“Magnus Henrikson
Chief Engineer at Scania
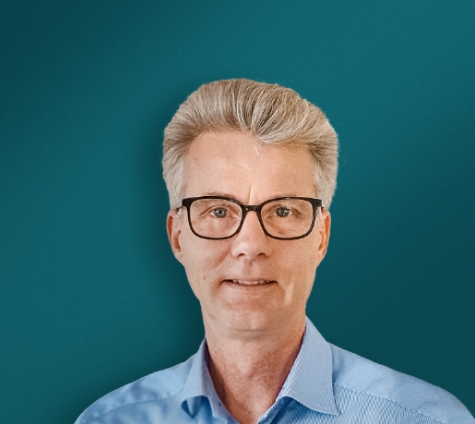
Magnus Henrikson, Chief Engineer at Scania
From a Scania engine to a TRATON engine
“We thought about a new engine for the first time back in 2008,” Magnus Henrikson, Scania’s Chief Engineer, recalls. “But things didn’t really get started here until the initial concept in April 2012.” Henrikson has been at Scania for 32 years, and was involved in the CBE from white paper to production. “The new engine was all about reducing fuel consumption and CO2 emissions,” the engineer explains. Development took a new direction at the beginning of 2015: MAN and Scania became “sibling” brands under the same parent company — and Henrikson was to develop the new engine together with colleagues from Germany going forward. “Working together was not easy at first, as both sides largely favored their own way of designing,” Henrikson reflects.
Thomas Nickels remembers this initial phase of the TRATON GROUP well. As the Head of Powertrain at MAN, he was responsible for representing MAN’s requirements during the concept phase: “We tried to get all the experts at Scania and MAN on board.” But the beginning of their collaboration was not without friction, and a number of joint workshops were held. “At the time, the exchanges between us were frequent and intense, and several things had to be redeveloped,” explains Håkan Johansson, who joined the project during this phase as the Head of Engine Development at Scania. “The Scania engine turned into a TRATON engine during this time. There were a lot of discussions, even some contentious ones, but we had a better engine in the end.” Compared to the first concept, the CBE is shorter and lighter, saves even more fuel, and costs less.
„At the time, the exchanges between us were frequent and intense, and several things had to be redeveloped.“Håkan Johansson
Head of Conventional Powertrain at Scania
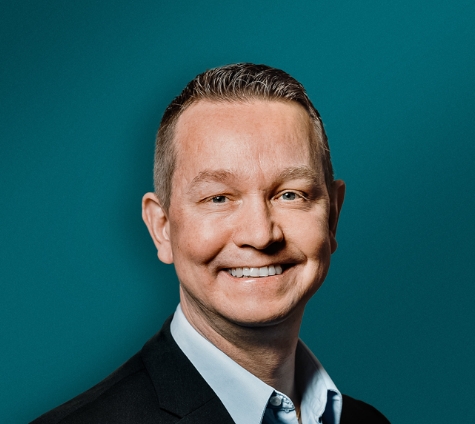
The same — but different
In addition to fundamental characteristics of the engine such as size, weight, and fuel consumption, how easy it is to integrate further down the line also plays a crucial role: “We focused on keeping the amount of effort it would take to integrate the engine in MAN vehicles later to a minimum,” Nickels explains. “That was a major challenge.” On the one hand, there were to be as many mutual components as possible, on the other — this was to have as little impact on the vehicle as possible. “The vehicles are quite similar if you look at them from the outside: they have the same wheelbase and the same dimensions,” Nickels continues. “But when you take a closer look, the vehicle design and application are quite different at Scania and MAN.”
The balancing act between as many joint components as possible and as little impact on the vehicle as possible affects not only the engine, but also the entire powertrain, of which the CBE is a part of. In the future, there will also be joint modular platforms for these elements for all brands as part of the Future Powertrain Program (FPP). In addition to the CBE, this includes the gearbox, aftertreatment (CAS) and rear axle (CAM). The engineers have to adapt the interfaces so that the engine and the entire powertrain can be installed in vehicles of the different brands. “For example, when I develop add-on parts for engines, I design them so that they are positioned in the same place for each brand if possible,” Nickels explained. The components have to meet the requirements of the respective vehicle without new variations of these parts being necessary. “That’s a big challenge.”
„We tried to get all the experts at Scania and MAN on board.“Thomas Nickels
Head of Electrification Development Group Industrial Operations TRATON SE, Senior Vice President Engineering Drivetrain, Cabin & Chassis (ED) MAN Truck & Bus SE
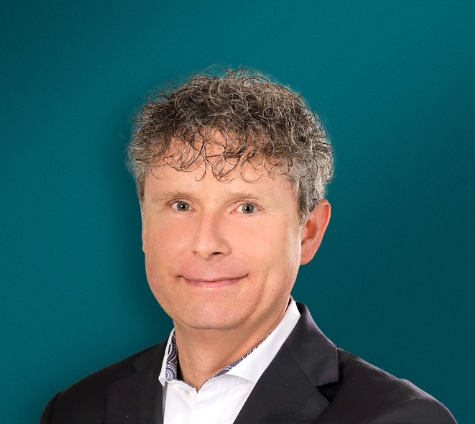

Darren Gosbee, Vice President of Engineering in research and development at Navistar
New platforms
For Nickels, however, it is definitely worth tackling this challenge and even expanding on it: “If we move to more extensive shared systems, say the chassis, then there is potential for even more considerable savings. For instance, the interfaces would no longer have to be adapted if we can align them for all brands. In turn, this would mean we could make the modular platform smaller, resulting in even less complexity and even lower costs.”
Navistar has also been involved in the CBE project since 2017. At that time, it was still a partner of the TRATON GROUP; since 2021, it has been a part of the Group as a subsidiary. The CBE comes with something called a long mount, but Navistar has traditionally used a short mount. “The difference is clear to see if you compare the front end of US trucks with the trucks in Europe,” explains Darren Gosbee, Vice President of Engineering in research and development at Navistar. This makes a different engine mount necessary. Navistar engineers have been working hard for the interfaces towards their products. And succeded! A modular platform is a good option for managing complexity: “We’re already thinking about how we can adapt our vehicle designs so that we can take on more shared parts in the future.” Until then, the goal is to learn more about modularity and to keep growing.
„We’re already thinking about how we can adapt our vehicle designs so that we can take on more shared parts in the future.“Darren Gosbee
Vice President of Engineering in research and development at Navistar
The future of modularity
The same interfaces and the smallest possible modular platform are also intriguing when it comes to e-mobility. In the commercial vehicle sector, in particular, range, which depends directly on the battery pack, is a big concern when it comes to electric vehicles. “When we take a look at how batteries are best installed, we end up back at the topic of the interfaces between components and vehicles,” says Nickels. “So we launched a great project in which we developed a joint modular platform for batteries and coordinated it with Scania, MAN, Navistar, and Volkswagen Truck & Bus.” This is one example of how the transition to e-mobility in the TRATON GROUP offers the opportunity to develop new products on a single platform rather than many different ones.
It will be a while before e-mobility is widespread everywhere, possibly as long as decades for some applications and in certain regions. While the CBE may be the Group’s last diesel engine, it is certainly not a model destined for obsolescence. The new jointly developed CBE will celebrate its debut on the road with Scania: the 460 R Highline is the first vehicle to be powered by this engine. In February 2022, this truck made an impressive showing by winning the renowned Europe-wide 1,000-point test. Navistar will introduce the CBE in 2023, with MAN to follow a year later and Volkswagen Truck & Bus planned for 2028. Compared with the engines it will replace, the CBE has a high efficiency of more than 50 percent. Fuel consumption is considerably lower and the CBE offers greater overall economy and significantly lower CO2 emissions.
The brands learned a great deal during the development of the CBE, and will continue to collect experiences throughout its introduction across brands and national borders. This will also benefit the TRATON GROUP in the future development of electric drive systems. And the Group has the opportunity to begin new developments on a modular platform, thus eliminating the time-consuming integration in different chassis. That will take the topic of modularity to the next level throughout the Group.