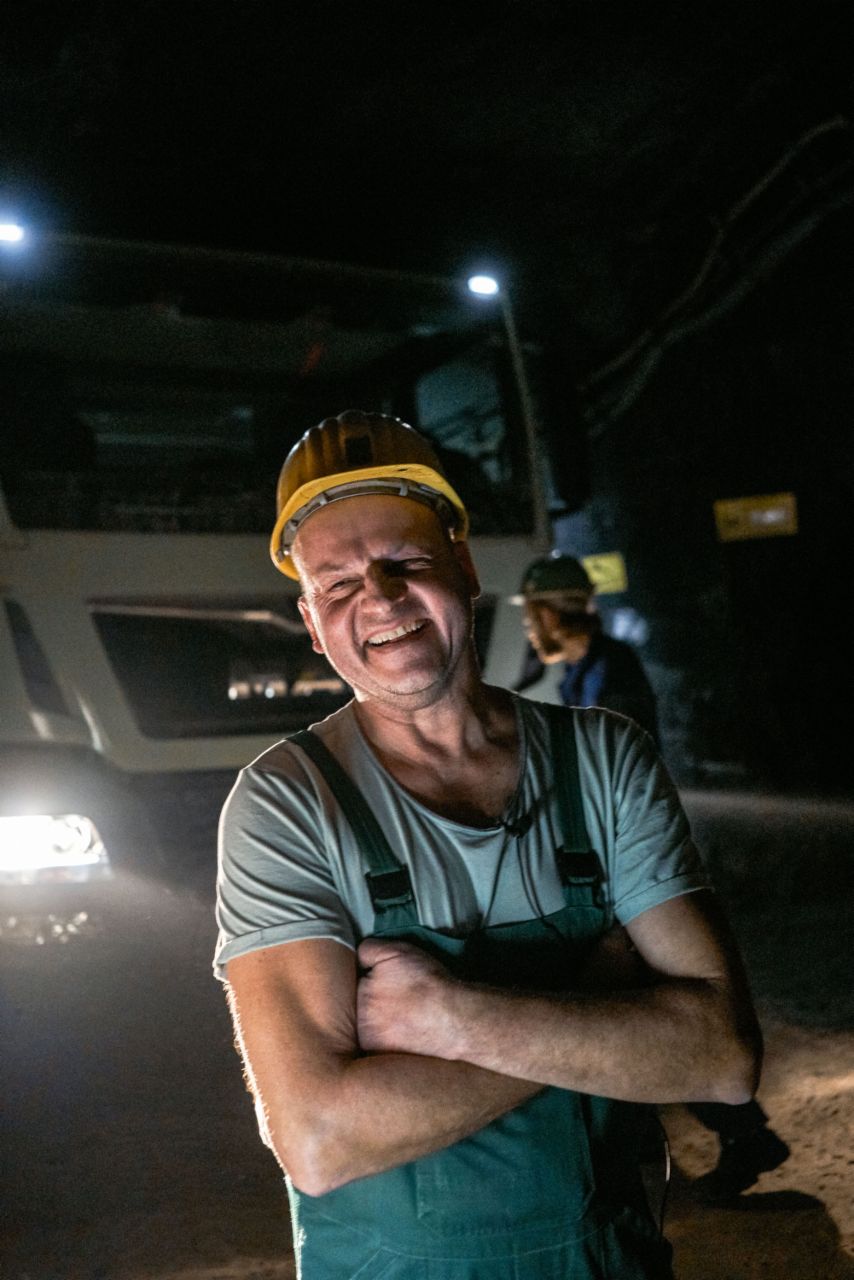
Around 5:15 a.m., underground: Matthias Wenzel slips into his green overalls, and grabs the pit lamp and his emergency oxygen supply. He gets into the iron cage, presses a button, and plunges into the depths. Pressure builds in his ears on the journey to the Earth’s interior; the temperature climbs to around 30° Celsius.
Two minutes later, Wenzel reaches the shaft’s fill position, 714 meters underground. The 49-year-old has been working here as a large equipment driver for three years. Previously, he worked as a trucker on the motorways and country roads of Europe. Now his driving territory is a dark track system that extends 14 square kilometers beneath the Earth’s surface. In all, 125 miners and 70 pieces of large-scale mining equipment and vehicles are deployed here, below and above ground. A ventilation system provides the mine with fresh air.
Wenzel opens the gate of the cage and walks to the Teutschenthal shaft’s fill position. The light of his pit lamp finds the outline of an MAN TGS with overlying dumper. Shortly after that, the trucker sets his vehicle in motion. In this subterranean landscape, the speed limit is 30 km/h. Some passages are filled so closely that Wenzel could touch the rock walls with an outstretched arm.
He stops at the so-called tipping cellar. Bulk material clatters from above into the dumper. “The truck won’t be this shiny for long!” says Matthias Wenzel, with a wry laugh. “But nobody down here will complain about a bit of dirt or a few scratches on the paintwork.” After a 20-minute drive, the truck approaches a tipping point. Wenzel uses the automatic sliding plate to push his load from the dumper into a cavity. Then he makes his way back, for the next trip.
“This transport really did come down to every centimeter.”
Uwe Müller – Operations Manager at Gress & Zapp
Protection against the risk of collapse
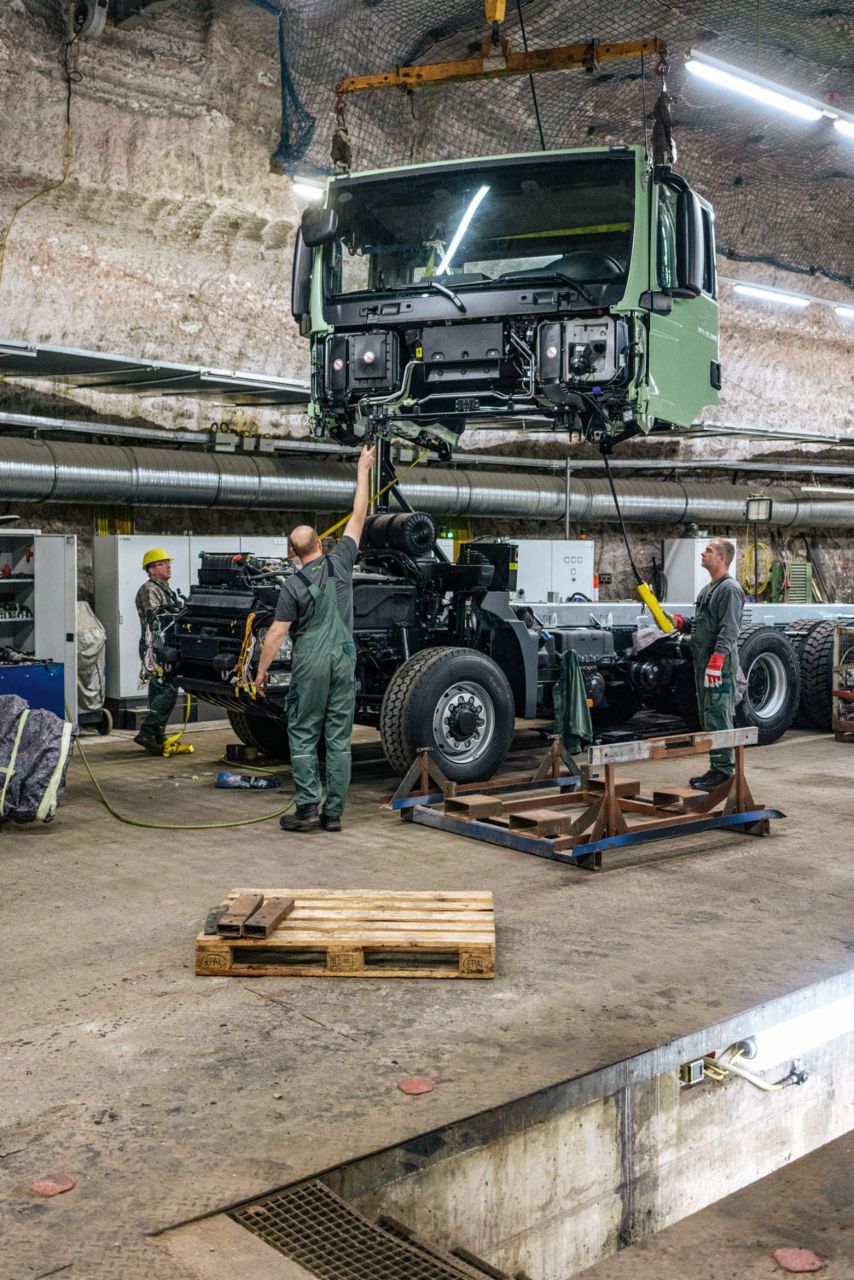
For over 75 years, miners near Halle an der Saale in Saxony-Anhalt have been extracting rock salt and potash—valuable mineral resources for producing, among other things, edible salt and fertilizers. Since the beginning of the 1990s, GTS Grube Teutschenthal Sicherungs GmbH has been securing the cavities, using suitable industrial mineral waste, known as offset. This protects the mine against dangerous rock falls, which have already occurred three times in its history. Truck driver Matthias Wenzel’s task is to transport the offset from the shaft to the necessary offset location and unload it there. His MAN truck was converted specifically for mine use, and he drives the route five times per shift, 18 kilometers back and forth.
A huge logistical achievement in transporting the truck underground had to be completed before the driver could sit behind the wheel of the TGS for the first time. The Gress & Zapp commercial vehicle service team worked on this task for around five weeks. Workshop fitters disassembled the cab, chassis and superstructure from the already drivable truck into several parts, and fixed them onto steel plates. Uwe Müller, Operations Manager at Gress & Zapp, directed the crucial steps above ground at the GTS Grube Teutschenthal site: a crane lifted the truck parts one after the other, gently setting them down upright on steel plates. Sparks flew while a welder spot-welded the support structures onto the plates. A forklift truck pushed the parts into the cage and the truck descended into the depths of the mine, where a second crane carefully pulled the truck parts out of the cage. “This transport really did come down to every centimeter,” Operations Manager Uwe Müller tells us afterwards, visibly relieved.
More traction, more payload
The truck was then rebuilt underground and approved by TÜV. Truck driver Matthias Wenzel was soon able to take his first trip. This is not just a standard TGS: the truck always drives fully loaded to its destination in the mine where the offset is unloaded, so the family business for special-purpose vehicle construction run by Toni Maurer fitted the original 360 HP three-axle vehicle with an additional lifting and steerable rear axle. “This makes the truck more agile than a conventional four-axle vehicle,” explains Managing Director Carl Mason. “It can maneuver better in the narrow sections and can also now operate with a higher permissible laden weight of 35 metric tons.” The HydroDrive with which the truck was equipped at the factory was another criterion for the Teutschenthal miners in deciding to purchase precisely this vehicle from MAN.
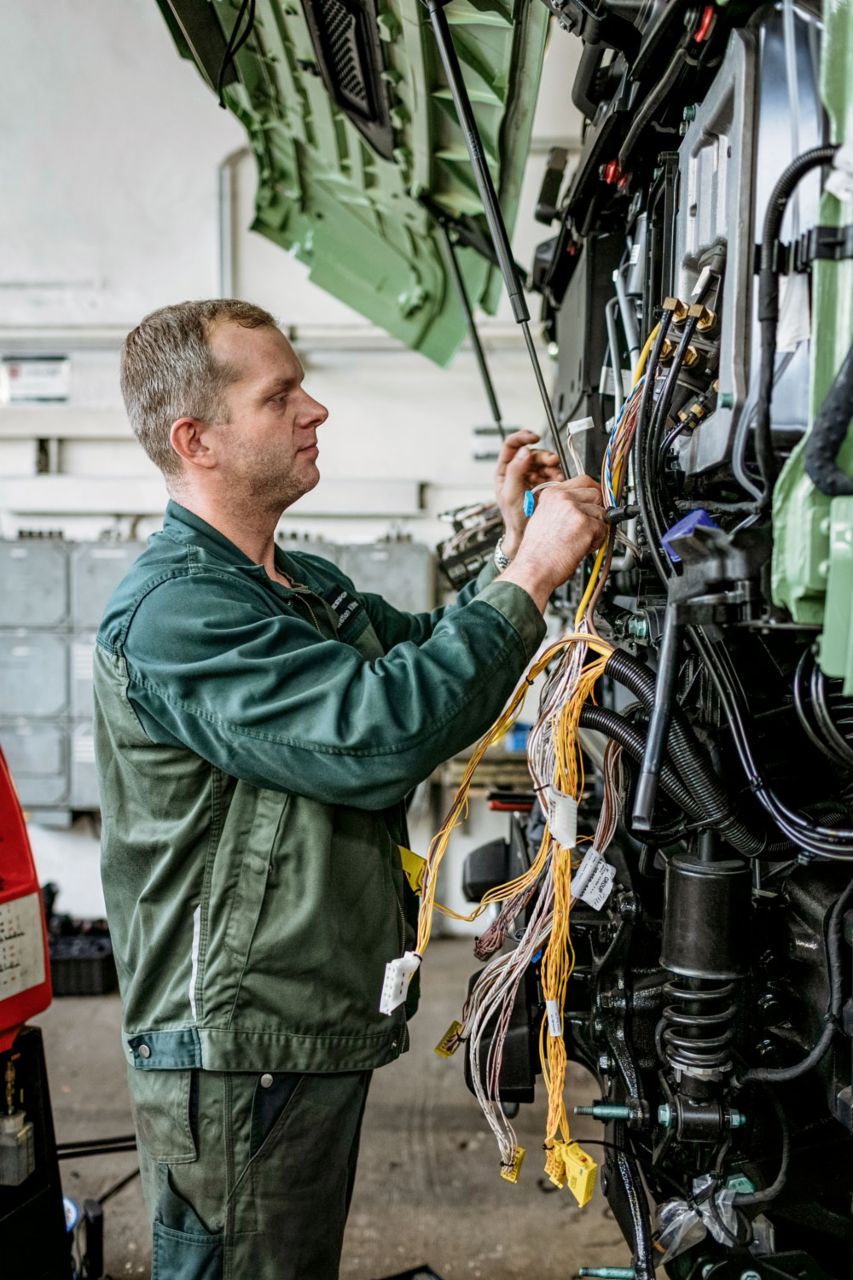
The reason is that the hydrostatic auxiliary drive on the front axle lends the truck key benefits. These pay off underground and make deployment there possible in the first place: the HydroDrive truck has a vehicle height of 3.05 meters, low enough to navigate the mine tunnels, which are only 3.60 meters high in parts. In contrast to conventional all-wheel drives, the HydroDrive does not require any additional ground clearance. It weighs less, offers more payload, and consumes less fuel than an all-wheel-drive truck. Yet the MAN HydroDrive has enough traction to cope with difficult surfaces. Driver Matthias Wenzel confirms this: “Some sections have steep uphill and downhill gradients. High ambient humidity makes the surface very slippery. I wouldn't be able to cope without the HydroDrive.” Its off-road capability means that the MAN HydroDrive also has fans beyond the mining industry. “It’s also suitable for use in gravel pits, on construction sites, and in forestry,” explains MAN expert Ralf Melbardis. More than 11,000 vehicles have been sold since 2005. One further modification was required to perfectly equip the truck for its tasks in offset mining: the driver’s cab has been sealed with silicone and equipped with an air filter system. This protects the driver, for example against dust emissions.
Sturdy enough for ten years of heavy work
The purchase is worthwhile for Thomas von Kalnassy, Technical Director at GTS Grube Teutschenthal and responsible for service and maintenance of its vehicle fleet. “This is the second MAN in our fleet. HydroDrive trucks are more efficient for underground transport tasks than conventional mining vehicles,” he says. Thomas von Kalnassy has calculated around ten years of underground service life for the new TGS. The truck will face heavy work on almost 250 days a year. It will travel around 200 kilometers a day and transport an average load of 25 tons, under driving conditions in the mine that are significantly harder than in normal road use. Offset mining is set to continue in Teutschenthal for around ten years, until the former mining chambers are completely filled. So Matthias Wenzel and his TGS will be kept busy. A colleague replaces the driver after his eight-hour shift, while the HydroDrive truck continues on its rounds in the darkness of the offset mine: powerful, agile, and tireless.
Figures | |
714 |
meters underground |
14 |
square kilometers of tunnel |
70 |
machines and trucks |
25 |
tons loading per trip |
Photos Michael Bader – Text Felix Enzian