The first electrically powered distribution truck in South America, the e-Delivery, is beginning series production in Resende, Brazil. In a pioneering initiative from Brazil to the world, Volkswagen Caminhões e Ônibus set up a completely new e-Mobility team and a whole ecosystem around the e-Delivery. This ecosystem is based on the e-Consórcio, a consortium with production partners and suppliers aiming to support customers throughout the electric vehicle’s life cycle.
At the beginning of 2018, Argel Franceschini, responsible for the Bus Engineering department at Volkswagen Caminhões e Ônibus (VWCO), took on a very special task. He was appointed as the engineering project manager in charge of transitioning the recently presented e-Delivery concept vehicle into series production. The demand came after the VWCO initiative that introduced a concept truck to investigate the potential of electric vehicles with customers in Brazil. Since the all-electric light-duty truck is the first of its kind, Franceschini and his colleagues from other departments had to integrate a new production line for these battery electric vehicles (BEVs) into the existing structures at the Brazilian VWCO plant in Resende — quite a challenging task of simultaneous engineering and manufacturing concept development. In the process, he quickly realized that to complete this endeavor, he would need to add new competences to the team. “It became clear to us that most of the competences we would need for this project cannot be found in the diesel industry, and a vast majority of the profiles we found were young people with a good basis in new technologies, who could help us to take the e-Delivery to series maturity,” the 37-year-old relates.
Now the brand new e-Delivery truck has been launched on the market, representing an important step VWCO and the TRATON GROUP are taking in their ambitious strategy for the electrification of the Group’s trucks and buses in the coming years. The e-Delivery covers a wide range of products in the light-duty truck segment, positioned as an important platform within the TRATON GROUP that complements its portfolio along with other brands like Scania, MAN, and Navistar.
Agile software development
Ana Fachardo joined the VWCO e-Mobility team as an electronic controls engineer. Since 2019, the 26-year-old has been responsible for the development, integration, and validation of the all-electric vehicle’s control unit. This piece of hardware, developed in collaboration with Bosch, is the memory and brain of the vehicle. It can register its every detail, making it possible to trace possible failures, for example. Additionally, the control unit interconnects the many different components of the electric truck. Ana Fachardo works together with 20 other team members, fully dedicated to new e-mobility systems like batteries and electric motors. The team is also supported by more than 50 other engineers responsible for the conventional truck systems like cabin, chassis, axles or suspensions. Developed together with the partners, the complex underlying software was repeatedly modified and further optimized during the testing of the e-Delivery — sometimes even directly on the test track.
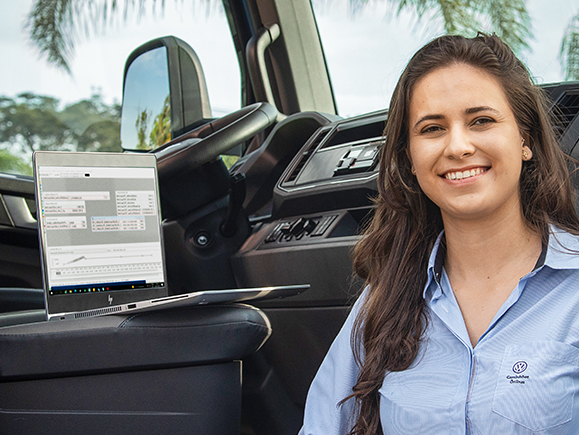
Ana Fachardo, electronic controls engineer at Volkswagen Caminhões e Ônibus
400,000kilometers was the distance over which Volkswagen Caminhões e Ônibus engineers monitored the e-Delivery prototype in test operation.
While pilot customer Ambev, a Brazilian brewery, was testing the first prototype in real-life applications, Fachardo monitored the software and controls of the prototype vehicles and put them through their paces during zero-emission tests over a distance of more than 400,000 kilometers. And even when production at the Resende plant was temporarily on hold during the COVID-19 pandemic, the team managed to keep the tests running. “We’re constantly making adjustments on site, on our testing ground,” she reports. Her coworker Franceschini adds: “The production of electric vehicles presents completely new challenges. One example is the battery technology: because the batteries keep on evolving, we have to make our product concept development and production process even more flexible.”
Converting production to e-trucks
The VWCO team saved valuable time and also mitigated the risks by developing the vehicle concept in a way that could allow the integration of the e-Delivery into the existing production facility, where VWCO manufactures around 350 other model variants in addition to the conventional Delivery. They succeeded because along with the simultaneous engineering, key partners at the plant are working in very close synergy and are responsible for their own production sections. “We’ve always worked in a production system called Consórcio Modular — that is, a close production network with our partners. You can think of it as several small factories, completely integrated within a larger production plant,” Franceschini describes.
The brand new modular architecture of the vehicle allowed for a very smart production setup, which in turn made it possible to convert the processes efficiently. The e-Delivery electric motor, for example, is a very compact unit that requires far fewer component modifications than a diesel engine, which has a lot more parts that are assembled on the powertrain assembly line. As a result, in order to optimize the usage of the production capacity, other auxiliary systems like the control units, air conditioning system, and pumps were installed in a structure that can be assembled together with the electric motor on the powertrain line. This means that the production process runs just as smoothly as with conventional truck models, maximizing production efficiency.
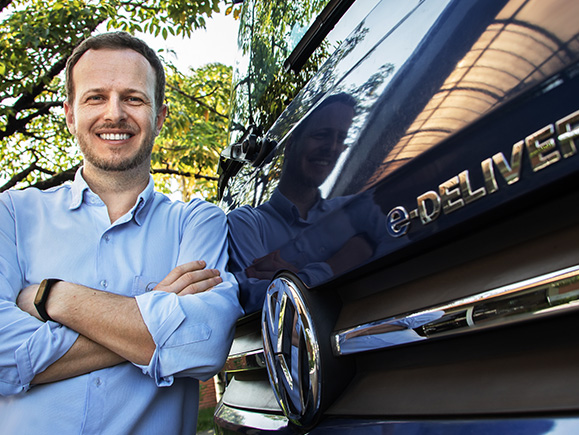
Argel Franceschini, manager of the e-Mobility area at Volkswagen Caminhões e Ônibus.
Battery assembly on site
The batteries are tailored specifically to the e-Delivery and are produced by CATL, one of the biggest battery manufacturers in the world that is based in China. “The battery specification, software integration, development tests, and structural validation were all major challenges for both VWCO and CATL engineering teams, who worked in close cooperation during the last 3 years to prepare the best solution in terms of performance, efficiency, and safety,” Franceschini says.
On the production side, the new e-Shop was added to the plant, a dedicated hall for high-voltage battery assembly and complete vehicle commissioning, located at the end of the assembly line. In this e-Shop, the e-Consórcio partner Moura installs the vehicle’s traction batteries, which are pre-assembled in a structure at its main plant in Pernambuco, 2,400 kilometers north of Resende.
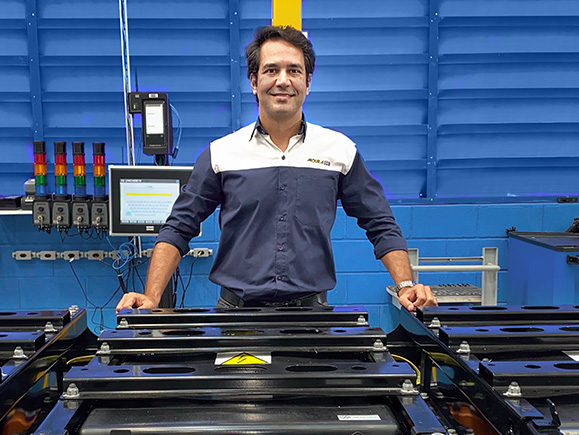
Fernando Castelão is responsible for the development of the lithium batteries for the e-Delivery at Moura, supplier and member of the e-Consórcio.
“It is always a magical moment when the e-Delivery is ‘energized’ with the battery.”FERNANDO CASTELÃO
Director Lithium Batteries at Moura
The man in charge of battery assembly, after sales, and the recycling process is 45-year-old Fernando Castelão, who heads the lithium battery business at Moura. “Equipping the e-Delivery is a big change for us,” Castelão says. In a car with an internal combustion engine, as he explains, the battery is mainly used for starting the vehicle. But in an electric car, it is the central component of the powertrain. For Castelão, it is always a magical moment when the almost finished e-Delivery is energized by the battery in the e-Shop. It takes seven skilled workers to energize the vehicles, and the same number of engineers and chemists are responsible for the pre-assembly at Moura’s main plant.
Wide-ranging cooperation within the e-Consórcio
The whole ecosystem around the e-Delivery extends far beyond the manufacturing process with partners, and that is where it differs significantly from the previous Consórcio Modular. To encourage the use of zero-emission electric vehicles in the logistics industry, the consortium also includes several companies such as Siemens and ABB, which are responsible for the charging infrastructure fleet operators’ facilities, as well as partner companies like GD Solar, which provide sustainable sources of energy generation — for example through solar energy systems on customers’ factory roofs or in dedicated solar plants. Franceschini stresses: “It’s crucial that we provide a complete ecosystem for our customers, including product, infrastructure, energy, fleet management, maintenance, recycling, and financial services. That is the core of the e-Consórcio concept.”
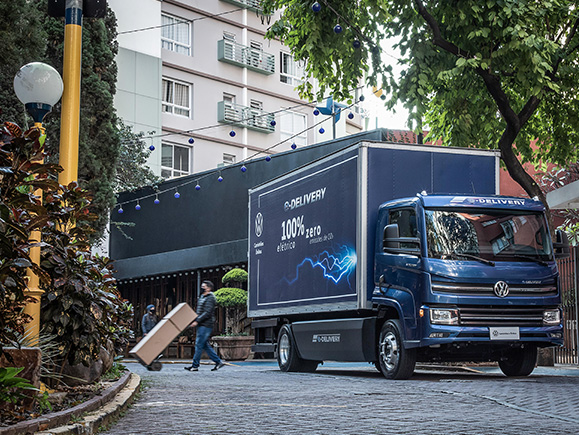
The start of production of the e-Delivery as the first fully electric truck in South America underlines the technological pioneering role of Volkswagen Caminhões e Ônibus, just in time for its 40th anniversary.
Modular platform and tests for the e-trucks
Volkswagen Caminhões e Ônibus (VWCO) developed a new modular architecture to support and serve as a baseline for the company’s electric trucks, creating more flexibility and making it possible to derive several variants from the e-Delivery baseline platform. This platform is divided into four modules: cab and auxiliary systems, batteries, suspension, and powertrain. VWCO can easily change components within a module, without the other ones being affected. The truck is developed around the batteries, maximizing energy capacity for higher range and efficiency, as well as giving high flexibility in the development process. In addition, a whole new set of tests was developed by the e-Mobility engineering team in order to perform the complete validation of the electric truck, ensuring reliability and safety of operations in the most challenging applications.
Franceschini also notes that for customers, everything is completely new compared to the diesel trucks they are used to working with. That’s why his team’s mission is to not only develop the electric truck, but also create the technical know-how at VWCO in order to improve customer support and experience. “The learning curve is still steep, and our mission is to share it with all the areas, partners, and customers involved,” Franceschini says. “Our vehicles provide us with ever-growing amounts of data from daily operations, which we use as a basis for further developments, focusing always on offering the best customer experience when operating our products and solutions provided through the e-Consórcio.”